If you have spent any time in the world of chemical process safety, the story of the Design Institute for Emergency Relief Systems (DIERS), an extensive R&D program sponsored by 29 companies under the auspices of AIChE, is likely a familiar one. Let’s take a look at the more utilitarian outcome of the DIERS undertaking, the development of the "Bench Scale Apparatus", the low thermal-inertia adiabatic calorimeter known today as the VSP2TM.
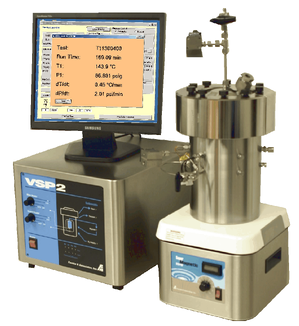
As we mark the 35 year anniversary of the original VSP, it begs the question: is the VSP2 still relevant in the world of process safety? It would be easy to say absolutely yes and just move on, but really one of the best ways to illustrate this view is to look at how the VSP2 revolutionized the process safety testing industry in the first place, to discern if that versatility continues to make it a viable and useful industry tool today.
A primary purpose of DIERS was evaluation of emergency relief system (vent) requirements, including energy and gas release rates for systems under upset conditions and the effect of two-phase flow on the emergency discharge (blowdown) process. Born of the DIERS testing methodology and further expanded upon in 1995, the VSP2 offers many innovative features that make it ideal for obtaining critical upset process design data including:
- Utilization of a light-weight test cell design (low thermal inertia) that is configurable to unique customer requirements for testing flexibility to simulate process conditions such as:
- Loss of cooling or agitation
- Accumulation or mischarge of reactants
- Contamination of batch
- Thermally initiated decomposition
- Resident incubation time
- In-situ liquid/gas dosing or sampling
- Unique heating system that prevents sample heat loss
- Temperature and pressure rise rates applicable to relief system design
- Automated Windows operation
- Compact modular construction for creative test design
- High pressure injection or metered injection of reagents
- Automatic pressure tracking
- Two-phase blowdown testing
Every day around the world the adiabatic data obtained with the VSP2 are directly applied to process scale to characterize reactive chemical hazards and risk consequences and to properly size emergency relief systems. The chemical industry continues to evolve with new products and new processes, but there remains an underlying need to know what will happen if things go wrong. Of course there have been tremendous advances in computational simulation since the VSP was first introduced, but setting aside the cost of developing a detailed runaway reaction and venting model even the best model is only as good as the data upon which it is built.
So, is the VSP2 still relevant? Absolutely. Industry never sits still, and the VSP2 continues to provide the foundation of critical upset process design data that is important to companies who seek to safely improve their processes as they build their business. Need more convincing? Perhaps the biggest indicator of the relevance of the VSP2 is the fact that it is still used extensively by industry-leading chemical and pharmaceutical companies around the world, including three systems in our own process safety testing laboratory.
Of course, in some thermal hazards applications the VSP2 is not the only tool that can do the job. In fact, at FAI we have a wide variety of complementary instruments in our own labs that we utilize based on the client application. But, in many cases today, we still find the VSP2 to be the most definitive and cost effective option.
As an industry leader, Fauske & Associates, LLC (FAI) is constantly seeking ways to improve our own products and the world of process safety, but rest assured that when considering if the VSP2 is still relevant the answer is a resounding Yes!
For more information, please contact us at info@fauske.com.