Radioactive Waste Consulting
Process engineering for safe storage of spent nuclear fuel (SNF) is a global challenge in which Fauske & Associates (FAI) is actively involved. For example, at the U.S. Department of Energy (DOE) Hanford site, metallic SNF in degraded condition has been stored under water at a location called the K West basin. This fuel is similar to the Magnox fuel stored at the Sellafield (UK) pond designated FGMSP, and in particular one route for remediation is to move the fuel from wet pond storage to intermediate-term dry storage. Wet storage of degraded fuel has evolved a large volume of uranium-metal bearing sludge, presenting unique challenges in developing potential remediation processes.

Table of Content
Expertise and Solutions
FAI has broad expertise in chemical issues that arise in decontamination and decommissioning (D&D) and nuclear waste technology. In particular, we have decades of experience in performing research and development to support remediation of the U.S. Department of Energy nuclear facilities. Our Waste Technology department has provided process engineering and safety support through analyses, software development and experiments for a wide variety of nuclear-chemical engineering issues.
Major project and facility applications related to spent fuel processing are:
- Idaho National Laboratory: Technical basis for aluminum/grout chemical reactions and hydrogen flammability; Dust explosion technical basis for mixed-waste treatment
- K Basins Closure at Hanford, SNF Particulate: R&D, process development and software development for spent nuclear fuel particulate vacuum drying
- K Basins Closure at Hanford, SNF Sludge: Process simulation for spent nuclear fuel sludge chemical/thermal treatment using FAI’s FATETM software
- Plutonium Finishing Plant, PFP/PRF at Hanford: Aerosol release basis for litigation, experiments and analysis explaining the PRF explosion accident
- Spent Nuclear Fuel Project at Hanford: Four of seven fundamental technical basis documents for passivation and storage of 2000 metric tons of damaged Uranium metal fuel; software for process safety, Uranium-metal reactions and pyrophoricity
- Spent Nuclear Fuel Sludge Project at Hanford: Chemically reactive sludge property technical basis; radiolysis, flammable gas and process analyses
- Nuclear Waste Tanks at Savannah River and Hanford: Adiabatic calorimetry and propagation tube experiments for chemically reactive waste; hydrogen mixing and solvent burning experiments; software for process safety
- Waste Encapsulation & Storage Facility at Hanford: Technical basis for Strontium and Cesium capsule disposition
- Waste Treatment Plant at Hanford: Explosive hazards analysis; due diligence and management transition; flammable gas design guide
- Waste Receiving and Packaging Facility at Hanford: Fire and source term analysis
Processing For Dry Storage
The most difficult SNF stream to process is a stream of metallic uranium particulate created from handling the damaged SNF elements. FAI has performed basic research and development on the physical and chemical processes unique to the vacuum drying of metallic SNF particulate. The purpose of the effort was to provide the technical basis for minimal design changes to an existing cold vacuum drying (CVD) process used for damaged SNF elements. (The earlier development of CVD process specifications for intact but damaged fuel was also supported by FAI.)
FAI addressed thermal stability of the SNF particulate using a graded approach beginning with simplified models and eventually including multi-dimensional transient calculations (see illustration below). The nature of thermal instability in particulate was found to be significantly different than for large SNF scrap pieces and highly damaged fuel elements. The end products of the effort were:
- Upgrades to the process simulation software FATETM to cover the dynamic range of metallic SNF particulate, scrap and fuel vacuum drying process design and safety analysis needs
- Independent reports containing details of the physical and chemical phenomena
- Verification and validation of FATETM with simplified methods
- Calculations for normal processing and accident scenarios for CVD of SNF particulate
A summary of the R&D effort is publicly available as “Physical and Chemical Processes During Vacuum Drying of Metallic Spent Nuclear Fuel,” Paper 59114, Proceedings of the ASME 2011 14th International Conference on Environmental Remediation and Radioactive Waste Management, ICEM2011, Reims, France, September 25-19, 2011.
Processes Considered for Vacuum Drying of Spent Nuclear Fuel Particulate
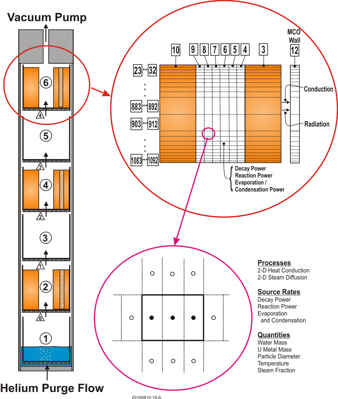
Sludge Handling
Processing of sludge that contains heavy, gas-generating embedded particles presents unique difficulties. In particular, such sludge has a high yield stress, so the gas generated inside a container of sludge cannot readily escape. Rather than rise through the sludge, gas bubbles tend to coalesce within the sludge, potentially growing into a much larger mechanically stable bubble that can displace the overlying material. This can have the unwanted consequence of plugging filters or even releasing sludge from the container.
Stable bubbles are clearly undesirable, so it is important to be able to predict bubble instability (breakup) and if necessary evaluate possible container design features that can disrupt or prevent the formation of stable bubbles. FAI has extensive analytical and experimental experience in analyzing nuclear waste tank sludge.
FAI performed basic research and development on the stability of sludge gas bubbles, using Taylor stability theory to develop a criterion for sludge bubble breakup. This predictive criterion was then validated by a series of experiments using various geometries and scales (see example illustrations below). Specific design features related to the container wall were evaluated to demonstrate their effectiveness at preventing or disrupting bubble formation.
Example Of a Sludge Stability Experiment to Predict and Prevent Gas Bubble Growth
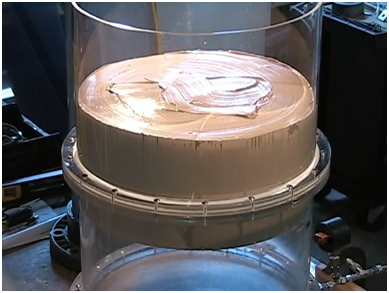
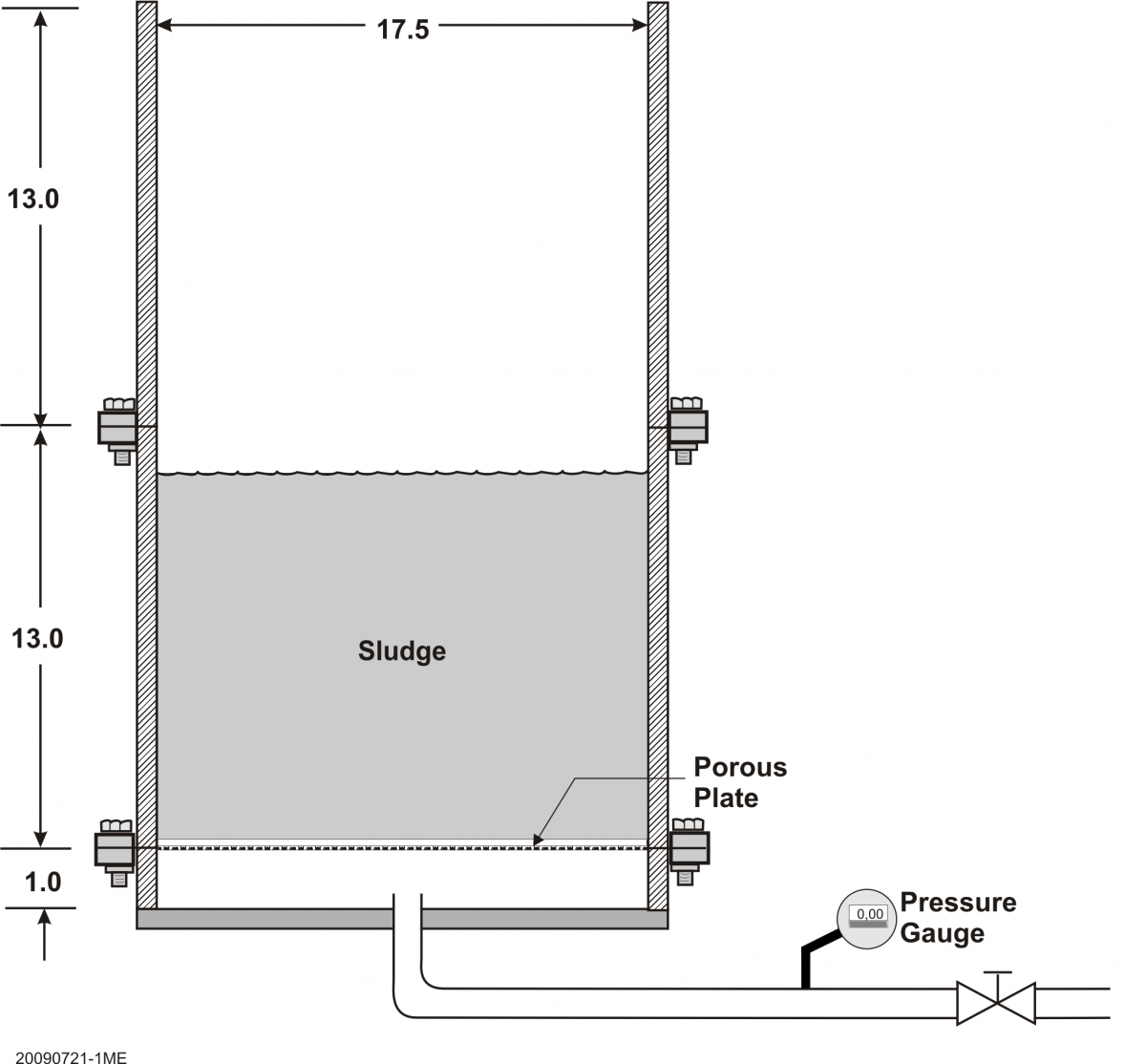