World Leader in Process Safety
Fauske & Associates uses a data-backed approach to solve complex process safety problems and prevent or mitigate accidents in the chemical and nuclear industries. We provide custom solutions including site assessments, full service testing, engineering, simulation, consulting, and training to nearly every industry from food processing to power generation.
Our Process Safety Experts Share Decades of Experience in Hazard Assessment and Testing

A site evaluation brings our safety experts to your facility to collaborate with your team in reviewing existing practices, equipment, and procedures. We determine your risk level and suggest ways to quantify or reduce risk, which often requires data on plant specific materials such as accumulated dust or reactive chemicals.

Our process safety laboratory provides critical data on combustible dust, gas, or vapors, or on any reactive chemical hazards identified during a site evaluation. We perform experimental simulation of credible "worst case scenarios" and can demonstrate the efficacy of proposed process improvements.

Based on the results of lab testing, we prepare a detailed report including our recommendations for process improvement, employee training, documentation, etc. If new safety systems are required, we work with you and vendors to develop an effective solution.
Our Solutions
Hazards Identification
The first step in ensuring process safety is to identify (recognize) potential hazards. Are you working with reactive chemicals? Is dust generated anywhere in the process? Any flammable vapors? It is hard to imagine an industrial process that does not entail some sort of hazard.
Hazards Characterization
Once potential hazards have been identified, it is essential to characterize those hazards. Not all hazards are the same, so you need to understand what you are working with. Metal dust and wood dust can both be hazardous but have different characteristics. Similarly, an organic peroxide tote and a monomer feed tank can both be hazardous but behave differently for example if exposed to an external fire. It is often not obvious which process hazards are the “worst case” so it is prudent to obtain test data from experimental simulation of the upset scenarios.
Hazards Mitigation
Process hazards can have severe consequences without adequate layers of protection. If an upset scenario cannot be prevented by procedural or design steps, then one must be prepared to mitigate the consequences. For example, one might take steps to minimize the risk of a dust explosion or a chemical runaway reaction, but there remains residual risk that can be mitigated by an appropriately sized pressure relief device such as a blowout panel or rupture disk.
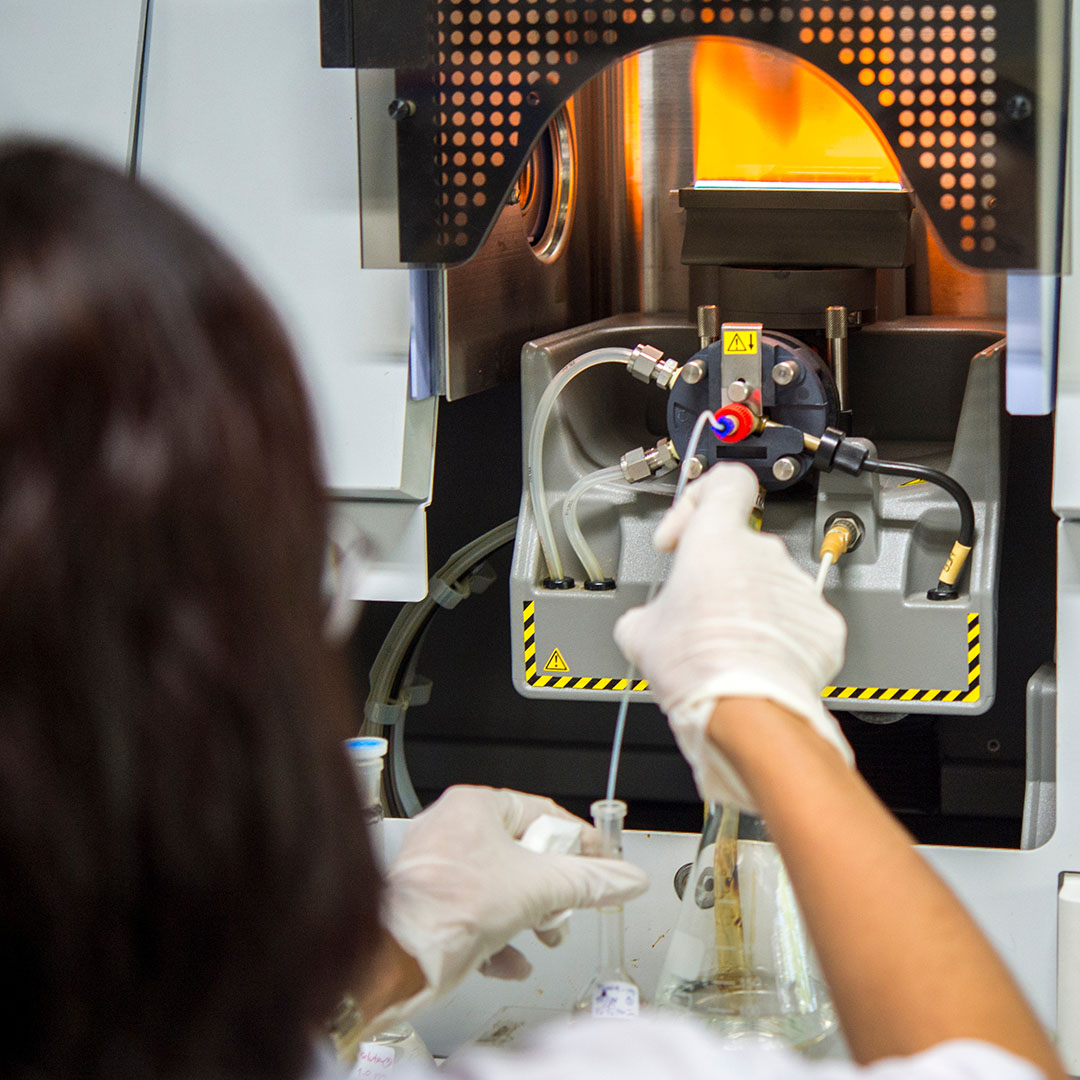
Laboratory Products
Vent Sizing Package 2 (VSP2)
Developed by FAI in the 1980’s under the DIERS research program to address the need for an adiabatic calorimeter with low thermal-inertia and a well-mixed sample (~80 ml). The VSP2 is suitable for directly scalable simulation of process upsets and runaway chemical reactions, functioning as a mini thin-wall chemical reactor enclosed in a protective containment vessel. Continuous pressure-temperature data during a chemical runaway facilitates parametric variation of relief set pressure when analyzing the adequacy of an existing pressure relief vent.
ARSST
The Advanced Reactive System Screening Tool (ARSSTTM) is a low thermal-inertia screening calorimeter, developed as a simplified alternative to the VSP2.
The ARSST quickly provides pseudo-adiabatic and directly scalable data for characterizing thermal and decomposition hazards using a smaller but still well-mixed sample (~10 ml) in a vented spherical glass test cell. It is ideal for energetic and gas generating reactions, and the data are amenable to simplified vent sizing methods.
FERST
The Fauske Emergency Relief Sizing Tool (FERST) powered by CHEMCAD is practical software designed to help you ensure that your chemical processes are adequately protected against overpressure from process upsets and runaway chemical reactions.
FERST is the complete package combining a practical and easy-to-use interface, straightforward calculation methods, the direct use of temperature and pressure rise rates from low ф-factor calorimetry data, industry standard DIERS two-phase flow models, and the material property, thermodynamic, and software development expertise from ChemstationsTM.
Our Process Safety Experts Share Decades of Experience in Hazard Assessment and Testing

A manufacturing company recognizes that there is dust in their process and is motivated by OSHA regulations to ensure their facility is safe. They work with FAI to perform a DHA and identify a number of locations where dust can accumulate. Samples are collected and tested at the FAI safety lab. Test results are used to prioritize housekeeping and process changes, and to install properly sized safety systems to mitigate potential dust explosions.

An innovative new chemistry is developed in the lab and there is pressure to scale-up to production as quickly as possible to take advantage of market opportunity. What could go wrong? Post-accident investigation noted that the process was scaled directly from 1 liter to almost 10,000 liter without recognizing the runaway reaction hazard potential and with an emergency relief system that was incapable of relieving the pressure from an unintended secondary exotherm following failure of the cooling system.

Decommissioning at a legacy government site is taking longer than planned, and an innovative approach is needed for safe packaging and storage of radioactive debris that accumulated over decades in an aging fuel storage pond. Oh, and the material is chemically reactive and generates hydrogen. A passive hydrogen venting design is invented and tested at full scale in the FAI flammability lab, enabling accelerated waste retrieval and direct storage in shielded boxes without an expensive processing facility.

An extended power uprate (EPU) at a nuclear plant led to unanticipated vibration in the main steam line. FAI collaborated with the utility, the valve vendor, and the Westinghouse BWR acoustic group to identify the root cause as vortex shedding in the main steam isolation valve (MSIV). FAI performed 1/5 scale tests which reproduced the Helmholtz instability and demonstrated that the problem was solved by simply adding "teeth" to the valve seat rings. The plant installed this fix and achieved full EPU.
Tailored Solutions
At Fauske & Associates, we offer custom testing and modeling services to validate analysis, quantify hazards, and help keep you safe.
Flash Point
Flash point is the minimum temperature at which vapors from a liquid pool form an ignitable mixture with air. Results help characterize a liquid as either being flammable or combustible based on the criteria of the NFPA, EPA, OSHA, or UN and identify the packaging and shipping group for transportation purposes in addition to storage and handling requirements.
Learn More About Flash PointAutoignition
Autoignition temperature is the lowest temperature at which a gas or vapor will spontaneously ignite without a distinct ignition source. This flammability property depends on various factors including pressure, temperature, oxidizing atmosphere, vessel volume, and fuel/air concentration.
Learn More About AutoignitionKST and PMAX
The explosion severity test generates the KST and PMAX values which are the explosive properties used to characterize a dust explosion. KST and PMAX represents the maximum explosion overpressure. These data tell you how much pressure an explosion will generate and how fast the explosion will travel.
Learn More About KST and PMAXMIE
The minimum ignition energy (MIE) is the minimum amount of spark energy needed to ignite an explosion of a dust in a suspended cloud. It is performed using ASTM E2019, “Standard Test Method for Minimum Ignition Energy of a Dust Cloud in Air” or EN13821 “Potentially explosive atmospheres — Explosion prevention and protection — Determination of minimum ignition energy of dust/air mixtures”.
Learn More About MIEVent Sizing
Vent sizing by direct scaleup requires adiabatic data from low thermal inertia devices like the VSP2 and ARSST. Measured rates of temperature and pressure rise during a thermal runaway define the volumetric rates of vapor and gas which must be discharged under emergency relief conditions, and these are readily applied to process scale using ERS design tools such as FERST which accounts for two-phase flow.
Learn More About Vent SizingThermal Stability
Our thermal hazards lab has a variety of instruments to test the thermal stability of condensed phase materials, including the ARC, DSC, TGA, TAM, and C80, and we are experts at using tools like AKTS software to evaluate process safety parameters such as time to maximum rate (TMR) and self accelerating decomposition temperature (SADT).
Learn More About Thermal StabilityLIRA
The Line Resonance Analysis (LIRA®) cable condition monitoring test provides both an indication of the overall cable health and as well as locally degraded areas. It is a non-destructive examination (NDE) tool that does not over-stress the cable.
Learn More About LIRACustom Testing
We have the experience and facilities to provide custom testing to solve your unique process safety problems. Our campus has multiple laboratories for testing chemical reactions, dust or vapor explosions, piping hydraulics, and electrical integrity. Our consultants will work with you to design a testing program to get the data you need to keep your process safe.
Learn More About Custom TestingFrom white papers to videos, we help answer your safety-related questions.
Our highly experienced team keeps you up-to-date on the latest process safety developments.
Stay informed with our quarterly Process Safety Newsletters sharing topical articles and practical advice.
With over 40 years of industry expertise, we have a wealth of process safety knowledge to share.
With over 40 years of industry expertise, we have a wealth of process safety knowledge to share.
With over 40 years of industry expertise, we have a wealth of process safety knowledge to share.