What is Risk Based Inspection? Related to Process Safety Management?
Introduction to Process Safety Management
Risk Based Inspections (RBI) are vital to employee and plant safety but how does it relate to your Process Safety Management (PSM)? We explore this topic in more detail on this page.
Table of Contents
1. What is Risk Based Inspection? Relate to Process Safety Management (PSM)?
- Benefits to having Risk Management Services to help an Risk Based Inspection
2. Combustible Dust Hazard Analysis (DHA) Explosion and Fire Hazard Evaluation
- On site safety inspections can identify possibilities for fugitive issues by providing the following services
3. NFPA and OSHA NEP Combustible Dust Compliance
- Additional services
- Process Hazard Analysis (PHA)
- Hazard Identification & Risk Analysis
- Consequence Analysis
5. Fire Protection Engineering
7. Process Safety Management (PSM) Program Development and Support
8. Relief System Design Review
- The Human Factor and Safety Culture
What is Risk Based Inspection? Relate to Process Safety Management (PSM)?
A Risk Based Inspection (RBI) is basically a risk analysis of operational procedures. It assesses the safety risks and plant integrity that exist and further prepares it for possible inspections. The end result is a document that outlines, measures and defines organizational procedures based on standards, codes and best practices.
Per Wikipedia, "RBI is most often used in engineering industries and is predominant in the oil and gas industry. Assessed risk levels are used to develop a prioritized inspection plan. It is related to (or sometimes a part of) Risk Based Asset Management (RBAM), Risk Based Integrity Management (RBIM) and Risk Based Management (RBM). Generally, RBI is part of Risk and Reliability Management (RRM)."
Generally, RBI's are used when a company wants to change the required frequency of inspection for pressure-rate vessels. This is applicable to the mechanical integrity element of a Process Safety Management (PSM) plan and one of the top most cited elements of OSHA.
Also per Wikipedia: "Process Safety Management is an analytical tool focused on preventing releases of any substance defined as a 'highly hazardous chemical' by the Environmental Protection Agency or OSHA. PSM refers to a set of interrelated approaches to managing hazards associated with the process industries and is intended to reduce the frequency and severity of incidents resulting from releases of chemicals and other energy sources (US OSHA 1993). These standards are composed of organizational and operational procedures, design guidance, audit programs, and a host of other methods."
The U.S. Occupational Safety and Health Administration (OSHA) 1910.119 defines all 14 elements of a Process Safety Management plan. Within the 14 elements is "Mechanical Integrity of Equipment":
"Employers must review their maintenance programs and schedules to see if there are areas where 'breakdown' is used rather than the more preferable on-going mechanical integrity program. Equipment used to process, store, or handle highly hazardous chemicals has to be designed, constructed, installed, and maintained to minimize the risk of releases of such chemicals. This requires that a mechanical integrity program be in place to ensure the continued integrity of process equipment.
Elements of a mechanical integrity program include identifying and categorizing equipment and instrumentation, inspections and tests and their frequency; maintenance procedures; training of maintenance personnel; criteria for acceptable test results; documentation of test and inspection results; and documentation of manufacturer recommendations for equipment and instrumentation."
Where there might be a bit of overlap/similarity in RBI and PSM is in the area of mechanical integrity with regard to structural engineering. Structural engineering is an important field of engineering that deals with the integrity of objects such as plant components or structures and serves the industry by performing analytical assessments, experiments, walkdowns or numerical modeling. Some companies specialize in supporting industrial process facilities and power plants.
In plants, the structural challenges are often related to pressure, temperature and dynamic forces. An example is the seismic adequacy of piping or components under power operation. Engineers perform seismic walkdowns on a regular basis to screen for the seismic adequacy of systems. Some companies are able to follow industry guidelines such as EPRI 1019199 “Experience-Based Seismic Verification Guidelines for Piping and Tubing”. Alternatively, some have developed their own seismic screening methodology which provides an even more cost effective and conservative assessment approach. Several specialty engineers and contractors have undergone professional seismic training which also allows them to assess safety-related electrical components such as instrumentation and control components, etc.
To support plant modernization and power uprate projects, for example, there is a need to utilize all facets of structural engineering. For example, we have seen an increasing demand for vibration analyses.
Increasingly, it is imperative to effectively study the cause of the vibration and to propose solutions for elimination or mitigation. Engineers are available for on-site support which includes measurement, troubleshooting and root cause analysis in a team setting together with the client.
Proper application of structural engineering expertise can help mitigate issues by ensuring that the plant and components are properly engineered. This will avoid machinery breakdown and costly plant outages. The goal is to support customers to achieve a safer and more efficient work environment along with enhanced plant durability.
Thus, for several aspects of RBI and PSM, an engineering firm with testing labs are ideal in providing a one-stop-resource for structural engineering issues including analyzing a problem, engineering a solution, verification, as well as oversight of fabrication and installation, as required.
Also within the PSM Elements defined by OSHA is Process Hazards Analysis (PHA) - a systematic evaluation of the hazards involved in the process. PHAs are required for initiation of a process and at least once every five years after that. It is important to address normal operating conditions as well as start-up, normal shut down and emergency shutdown procedures during the PHA. The PHA team should be multi-disciplinary, including operations, engineering and maintenance. To properly conduct a PHA, the process safety information (PSI) must be as complete as possible.
In response to continued rapid growth in safety needs for the chemical, nuclear and other industries, a few process safety engineering labs offer a complete range of Risk Management Services (RMS) such as Combustible Dust Hazard Assessment (DHA) Explosion and Fire Hazard Evaluation, Process Hazard Analysis (PHA), Hazard Identification Risk Analysis, Consequence Analysis, Safer Process Scale-up, Process Safety Management (PSM) Program Development, and Relief System Design Review to name a few.
Benefits to having Risk Management Services to help an Risk Based Inspection
- Understand and address hazards that pose the highest level of risk to your process facility
- Ensure compliance with relevant national, local and industry standards
- Implement best engineering practices
- Reduce overall level of risk
- Increase productivity and employee morale
- Make organization more competitive
- Chemical process safety
- Decrease insurance premiums
Combustible Dust Hazard Analysis (DHA) Explosion and Fire Hazard Evaluation
Experts provide onsite Combustible Dust Hazard Assessments (DHAs), Process Hazard Analyses (PHAs), OSHA Combustible Dust NEP compliance support, training and other services related to characterizing, preventing and mitigating combustible dust explosion and fire hazards. An onsite assessment provides an experienced engineer to visit a facility, evaluate its compliance with relevant national, local and industry standards and provide recommendations for risk reduction. Additional services can include deflagration vent sizing calculations, desktop reviews, equipment selection guidance, training of personnel on combustible dust hazards as well as development of process safety programs to address the

issues.
Industries affected by potentially hazardous dust are food, agriculture, wood/paper, metal processing, pharmaceutical, plastics/polymers, textiles, cosmetics and more. Every step of manufacturing or handling materials should be evaluated for potential interaction with simple static electricity, overheating of adjacent equipment, proper sizing of dust collection units and frequent evaluation of any changes in processes that could make a previously safe operation suddenly unsafe. Dust explosions can occur when debris wafts into the air in the right conditions, is blended in a new way, changes particle size, is insufficiently collected, comes in contact with unexpected heat sources and so on. Simple Go/No Go tests can indicate quickly what potential hazards you might have in a small sample size.
On site safety inspections can identify possibilities for fugitive issues by providing the following services:
- Incident investigation for dust explosions and fires
- Evaluate compliance with relevant national, local and industry standards
- Electrostatic hazards – e.g. grounding and bonding issues
- Recommendations for explosion hazard risk reduction
- Identify dust sampling points and collect samples for dust explosibility testing
NFPA and OSHA NEP Combustible Dust Compliance
- Preparation for an OSHA Combustible Dust NEP inspection, including appropriate responses to inspector’s questions
- Perform a Process Hazard Analysis (PHA)for compliance with NFPA
- Documentation review for NFPA and OSHA Combustible Dust NEP requirements
- Testing services to meet all NFPA and OSHA Combustible Dust NEP requirements
- Conduct employee training to comply with OSHA Combustible Dust NEP requirements
Additional Services
- Vent size calculations for new or existing equipment (American and European standards)
- Ignition source evaluation (NFPA 654 and 77)
- Electrical area equipment classification (NFPA 499)
- Integration of combustible dust hazard management into existing process safety programs for process safety management (PSM)facilities
- Development of process safety programs to manage combustible dust hazards for non-PSMfacilities
Testing and Analysis
Process Hazard Analysis (PHA)
Process safety professionals can provide PHA services including PHA auditing / review, revalidating PHAs and facilitation. Some perform PHAs for compliance to OSHA PSM requirements as well as combustible dust related PHAs for compliance per National Fire Protection Association (NFPA) guidelines: NFPA 654, NFPA 664 and NFPA 484.
Look for an organization that can provide a full range of PHA services, using a variety of techniques including, hazard and operability (HAZOP) analysis, what-if, checklists, failure modes and effects analysis (FMEA) as well as quantitative risk assessments such as layer of protection analysis (LOPA).
Hazard Identification & Risk Analysis
Consulting services to identify hazards related to the handling or storage of flammable and combustible liquids and gases, combustible dust and reactive chemicals may be needed for your organization. Extensive testing experience provides the ability to identify potentially hazardous conditions that may not be readily discernable.
Consequence Analysis
Experts can evaluate the effect of various process upset scenarios including fire and explosions, vessel overpressure scenarios, chemical reactivity concerns, vapor cloud dispersions and chemical releases. Computer models may be used in conjunction with appropriate data to determine the effects. The benefit or risk reduction of safeguards or mitigation strategies can also be evaluated.
Fire Protection Engineering
Provides life safety and fire protection consulting, engineering, and design services to architects, owners and developers, construction teams and facility operators. Helps clients to understand and achieve essential life safety goals like complying with codes, meeting egress requirements, choosing sustainable fire protection systems, analyzing hazards, and preparing for and responding to emergencies. Why? Risk mitigation; help to lower design, construction, and operating budgets; and ensure enhanced safety for end users. May include:
- Building and fire code consulting
- Means of egress evaluation
- Plan review
- Commissioning and construction management services
- Fire modeling
- Explosion modeling
- Dispersion modeling
- Quantitative risk analysis
Safer Process Scale-Up
Also seek services for safer scale-up of batch, semi-batch and continuous processes. Consultation is available for process development groups involved in the scale-up of chemical processes throughout the development cycle. Areas of expertise may include the following topics:
- Onsite or desktop review
- Determine critical process parameters to avoid or mitigate unwanted reactivity
- Development of customized scale-up program designed for safer operation at various stages
- Perform calorimetry testing to characterize desired and undesired reactions
- Identify safe operating limits for temperature, pressure and other safety-critical parameters
- Emergency relief design calculations for pilot plant, kilo lab and commercial scale equipment
- Independent safety assessment
Process Safety Management (PSM) Program Development and Support
Seek a review or develop a process safety program to support chemical manufacturing facilities or development programs. This can be performed for facilities including a kilo lab, pilot plant, medium scale and commercial scale plants. Services/needs might include:
- Auditing, reporting and presenting
- Gap assessment to identify and prioritize needs
- Process validation
- Safe scale-up guidance
- Development report documentation
- Consulting on process safety issues for change control (management of change)
Relief System Design Review
Look for experts in the Design Institute of Emergency Relief Systems (DIERS) research project team. Those who participate in the DIERS users group and contribute to developments in relief system design technology provide testing experience and the unique capability to consult on this topic with proficiency. Your organization may need:
- Third party review of existing relief system design
- Provide cost-effective solutions if existing relief system design is not adequate
- Ensure current design basis is appropriate and credible
- Develop / review pressure relief guidelines
- Specialists in effluent control for two-phase flow systems
Training
Professionals are happy to train your staff in the understanding of technical issues, process safety programs or audits, regulations and more. Look for organizations that perform process safety audits as part of a comprehensive hazards analysis and can work with you to make sure your staff is supplied with training needs in many ways including:
Level I - Gap Analysis
Level II - Training & Consulting
Level III - Program Development and Implementation
Partial List of Services To Seek in an Engineering and Testing Lab: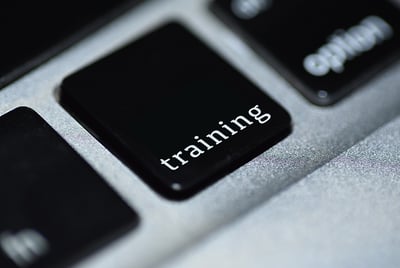
- Reviews and upgrades of all your safety process systems and regulatory requirements
- VPP Consulting
- Audits, reviews, and upgrades of all your Operating, Safety, and Maintenance Procedures
- Training program evaluations for both completeness and effectiveness (from technical skills to professional development) and upgrades where needed
- Reviews and upgrades of your program elements such as Employee Participation and Process Safety Information for effectiveness and completeness
- Work process effectiveness evaluations and upgrades
- Overall organizational development (e.g., motivation, work processes)
- Stress reduction
- Evaluations of the effectiveness of communication
Your organization may benefit from design, custom development and delivery of site specific training materials needed. Engineers and technical specialists are available to deliver the classroom, lab or on-the-job training your staff needs. In addition, they can assist with the identification and procurement of commercially available training materials where available.
Case Studies and Examples
For practical examples of some of these risk based inspection activities in action, please read “Case Study: A Risk-Based Approach for Combustible Dust Hazard Mitigation” by Timothy L. Cullina, P.E.*, Ashok G. Dastidar, M.B.A, Ph.D. and Amy E. Theis, P.E., Fauske & Associates Department of Risk Management Services.
- Hazard Identification: Material Properties and Process Description
- Gap Analysis including:
- Protection for equipment handling combustible dust;
- Electrical area classification; and
- Safety management systems that are not current or do not exist.
Process Hazard Analysis (PHA)
Using a well-defined testing strategy, gap analysis and PHA provided plant personnel an opportunity to understand hazards not previously realized and to determine the relative risk associated with those hazards. This approach engendered new ownership of the individual issues by the plant staff. By performing the gap analysis and PHA, a risk-based approach was applied to achieve and acceptable level of risk by implementing protective systems and safeguards. The PHA allowed the client to prioritize actions and assign responsible personnel to address recommendations and follow through on implementation. The client retained FAI to complete the same process at each of their other facilities.
Because of the unique work we do in the fields of safety for chemical process, combustible dust, flammability, nuclear and other industrial areas, we are constantly able to cross examine and engineer, test and consult with new applications and capability. For more discussion or information, please contact AnnMarie Fauske, afauske@fauske.com, 630-887-5213.
The Human Factor and Safety Culture
We wrote a blog a few years back “Improving Process Safety with Safety First Focused Culture”:
“A culture of safety is an ideal that should be ingrained in the overall organizational culture and reinforced daily from the highest levels of the organization all the way through the ranks. It incorporates numerous traits including leadership safety values, problem identification and resolution and personal accountability to name a few.4 Our management has long held the belief that in order to be successful as a business, we must put safety first. It is also a point that the management and founders of our company continue to reiterate to employees and clients and colleagues.
Fauske & Associates (FAI) founders Dr. Hans Fauske and Dr. Robert Henry gave the following response when asked to talk about what they see as the biggest change for the near future of process safety based on what they have seen to date?:
Dr. Fauske:
“The biggest change that I would like to see is basically making process safety a number one priority, even before profit. That’s a tough one, but I think it’s needed. I talk to a lot of people, customers and so on, and they say, ‘you well know the upper management isn’t willing to spend the money, it’s too costly.’ But it really comes down to a culture of safety. You need to have a safety process in a company, and you need to practice it, not now and then, but all the time. And particularly it has to come from up above, the president, the chairman or whoever is the top guy. It’s very important. And, I think if you are going to improve the industry from a safety point of view that’s got to take place.”
Dr. Henry:
FAI, we have seen first-hand the benefits of a strong safety first culture, operating on a motto of ‘safety is the priority, quality is the standard’. This dedication to safety has enabled us to establish a reputation of being a world leader in nuclear and chemical safety and to continue to count numerous industry-recognized experts as team members. A testament to this is that in the past 25 years we have had just 1 missed day(s) incident and have seen extensive business growth from a company with 2 business lines at the beginning to one now providing 14 business lines with offices and testing facilities spread across four buildings. Not to mention that our strong safety first culture has resulted in better quality products and service which has enabled us to consistently provide the excellent customer service our clients and partners have come to expect.”
About the Author
AnnMarie Fauske, MBA, is the Customer Outreach and Digital Media Director for FAI. Her career includes public relations for government, business, educational and non-profit campaigns and customer service education. Follow her weekly blog. She welcomes industry discussion, sharing FAI’s expansive expertise in the safety fields.