My Three Favorite New Features in FERST
As an engineer in Fauske & Associate’s Thermal Hazards Group, I am fairly well versed in the area of emergency relief system design; and I am certainly aware of some of the aspects that make it, at times, difficult and time consuming. When my colleagues announced the development of our new tool, FERST powered by CHEMCAD, I can honestly say our team was ecstatic. I want to share with you a few of my current favorite aspects of this software that has made emergency relief system design much easier (they say you should always work smarter not harder, right?!).
1 - Built-in DIPPR Material Properties
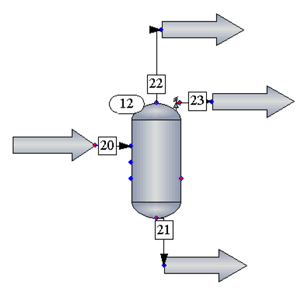
FERST powered by CHEMCAD allows the user to input user-specified material properties (helpful when relieving materials are unusual or exact experimental data on the material properties are available). FERST can now automatically generate the required material properties at the relieving conditions based on user selected components. This is an excellent feature, and it allows me to rapidly determine the effect of changing the set pressure on the relief requirements or to determine the worst-case venting situation. FERST powered by CHEMCAD uses the most up-to-date DIPPR database for the pure component properties and provides many different thermodynamic and mixing models for mixtures or materials with unknown properties.
2 - Clear Outputs for Describing New Relief System Designs
If a new relief system design is your goal (whether that means a new build or maybe you are moving vessels and need new or alternative relief piping), the Design output of FERST is going to be a huge help. This mode of FERST operation utilizes the Leung-Omega methodology with the most recent Leung-Omega correlation and a single set of equations to determine the mass flux for hybrid, gassy, or vapor systems. The solution to these governing equations provides the ideal vent area required. This means that in a perfect world without any frictional losses, this is the required flow area of your relief vent in order to protect your vessel from over pressurization.
Since frictional losses will always be present, FERST takes the results a step further and provides recommendations for the relief vent you should actually install. If you select a rupture disk, FERST will let you know what the actual relief orifice area should be, and the maximum amount of frictional losses (i.e., velocity head losses) you can install in the relief vent. If you are interested in installing a pressure relief valve, FERST will tell you what API orifice size you need, as well as the estimated maximum amount of inlet and outlet frictional losses your relief system valve can accept to satisfy the 3% inlet pressure loss and built-up backpressure requirements. This is an easy first step for any new design.
3 - Easy Evaluation of Existing Relief Systems AND Clear Outputs for Downstream Effluent Handling Parameters
There are many different situations where you need to evaluate the adequacy of an existing relief system; for example, when performing new chemistry in an existing vessel, switching vessels to increase capacity, making a process change, if a new upset scenario was identified during a PHA, after acquisition of a new plant, etc. Luckily, with FERST’s Rating mode, it is easy to input the information of a currently installed relief device (for either a rupture disk or relief valve) as well as information on the relief piping.
The output file provides the expected maximum pressure your vessel will experience for this scenario. This allows you to compare this pressure to the maximum allowable accumulated pressure (MAAP) to determine the adequacy of your relief system. Besides this crucial piece of information, the FERST output also provides key parameters (e.g. peak temperature, discharge two-phase density, discharge mass flow rates and flux, etc.) that you can easily use to evaluate additional downstream elements such as flares, quench tanks, knockout tanks, or for completing structural analysis on the relief piping.
Our team is constantly working to improve the software and bring in even more exciting features to FERST, and all of these updates are included! Some of the features I am most looking forward to are dynamic vessel venting and the capability to model multiple vessels venting simultaneously. Please contact us for a demo!
Reach out to the Thermal Hazards group for any of your relief system design needs or to learn more about FERST powered by CHEMCAD.
Contact us for more information!