Combustible Dust Hazard Analysis and Testing
Hazardous Dusts /Combustible dust hazards are common in industry and have gained additional exposure due to the OSHA Combustible Dust National Emphasis Program (NEP) which was re-issued as a result of the fatal accident at Imperial Sugar.
Fauske & Associates (FAI) offers a wide range of services related to a Dust Hazard Analysis (DHA) including identifying, characterizing, and mitigating combustible dust and fire hazards. These services include combustible dust testing, onsite assessments, OSHA and NFPA compliance assistance, audit preparation, training, ignition source evaluation and vent sizing calculations.
Our process safety professionals have served clients in a variety of industries including metal processing, wood/paper products, agriculture, food products, textiles, plastics, pharmaceuticals and many others.
Combustible Dust Hazards - Video Guides
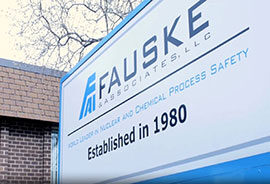
How to Collect a (Potentially) Combustible Dust Sample
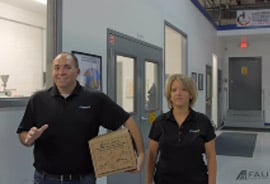
Combustible Dust Hazard Analysis (DHA) Sample Prep and Screening at Fauske & Associates
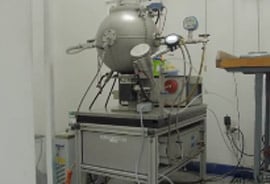
Combustible Dust Hazard 20L Chamber Go/No-Go Test, Explosion Severity Test, LOC, MEC, Pmax, MIE Test
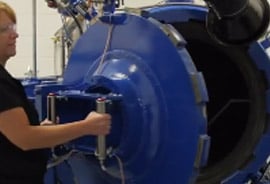
The 1 Cubic Meter Chamber — Characterizing Material for Dust Hazard Analysis DHA
Table of Contents
Knowing Your Risks
When developing mitigation strategies for potentially hazardous, explosive or combustible dusts, it is important to characterize the hazard risk of the material in question by determining its explosion severity and ignition sensitivity.
Explosion severity data will determine if an explosion hazard exists and, if so, how energetic it may be while ignition sensitivity data will assess the probability of risk based on how the material responds to heat, spark, impact and frictional forces.
Fauske & Associates (FAI) offers the following NFPA, OSHA and NEP Combustible Dust Hazard Assessment (DHA) testing and services for determination of both explosion severity and ignition sensitivity per ASTM and European EN methods.
NFPA & OSHA Combustible Dust NEP DHA Testing Services
Explosion Severity Test - (KSt ,PMax and dP/dtMax)
- ASTME 1226 – 2010 - Determines values necessary for designing protective measures, such as deflagration venting
- EN14034 - Part 1:2004 - Determination of the Maximum Explosion Pressure (Pmax) of Dust Clouds – Part 2:2006 - Determination of the Maximum Rate of Explosion Pressure Rise (dP/dtMax ) of Dust Clouds
Minimum Ignition Energy - (MIE)
- ASTM E2019 - Standard Test Method for Minimum Ignition Energy of a Dust Cloud in Air
- EN13821:2002 - Potentially Explosive Atmospheres - Explosive Prevention and Protection - Determination of Minimum Ignition Energy of Dust/Air Mixtures
Minimum Explosible Concentration - (MEC)
- ASTM E1515 - Identifies the Minimum Hazardous Concentration of a Dust Cloud that will Sustain Combustion
- EN14034-3:2006 - Determination of Explosion Characteristics of Dust Clouds - Part 3: Determination of the Lower Explosion Limit (LEL) of Dust Clouds
Minimum Autoignition Temperature of a Dust Cloud - (MIT)
- ASTM E1491 - Determines Safe Operating Temperatures at Which a Dust Cloud Will Not Autoignite
- EN50281-2-1:1999 - Electrical Apparatus for Use in the Presence of Combustible Dust - Part 2-1: Test Methods - Methods for Determining the Minimum Ignition Temperatures of Dust
Hot Surface Ignition Temperature of Dust Layers - (LIT)
- ASTM E2021 - Identifies Dangerous Operating Temperatures at Which a Dust Layer Will Self-Heat
- EN50281-2:1999 - Electrical Apparatus for Use in the Presence of Combustible Dust - Part 2-1: Test Methods - Methods for Determining the Minimum Ignition Temperatures of Dust
Limiting Oxygen Concentration - (LOC)
- Defines Safe Nitrogen Inerting Levels to Prevent Dust Cloud Explosion
- EN14034-4:2004 - Determination of Explosion Characteristics of Dust Clouds - Part 4: Determination of the Limiting Oxygen Concentration LOC of Dust Clouds
Testing is completed on-site in our state of the art dust testing facility per ISO 17025 guidelines.
Combustible Dust Hazard Basics, Part 1: What Does A Go/No-Go Test Mean?
Very often, when performing dust and explosibility testing quotes for customers, we are asked what exactly a Go/No-Go test is? While we offer a list of testing services to determine the deflagration hazards of dust samples per ASTM (American Society of Testing and Materials), OSHA (Occupational Health & Safety Administration, NFPA (National Fire Protection Agency) and UN (United Nations), knowing what this basic test is can go a long way for tackling your safety needs.
In order to "screen" for the possibility of dust explosibility in your facility, we perform a Go/No-Go Screening Test. Based on ASTM E1226, "Standard Test Method for Explosibility of Dust Clouds", this test is an abbreviated set explosion severity method with three dust concentrations to determine if the sample is explosible. This test is generally performed with samples tested "as received" or sieved with a 40 mesh (420μm) screen and using one 5-kJ chemical igniter as the ignition source. [>100 grams (~¼ lb) of sample less than 420μm required]
In the article: "How To Collect and Ship Combustible Dust Samples For Testing", we discuss the simple steps for getting your samples to a lab for testing. See above for our chart that depicts the outcomes
But, what if your Go/No-Go test result is a "no"? Well, we next look at what temperature it will take make your dust layer ignite. To find the Minimum Autoignition Temperature (MIT) of a dust cloud in the air, the MIT tests the minimum temperature that would cause your dust cloud to ignite. Next, is the LIT Test, which determines the hot-surface ignition temperature of dust layer. Finally, a Burn Rate test is conducted to determine how quickly the dust material will burn.
All of these tests start with the Go/No-Go Test. A comprehensive DHA or Process Hazards Analysis (PHA) can apply your test results to real world scenarios at your facility. Better to know wha t you are dealing with so you can plan safely! In addition, if you have a dust collector and aren't sure what to do next, read: "Combustible Dust Made Easy".
Here are some other tests run for dust explosibility screening:
- Combustible Dust Hazard Screening Test - Based on VDI2263 and UN 4.1 combustion testing. This test is to determine if a dust in a pile supports self-sustaining flame propagation. [>30 grams(~1oz)of sample less than 420μm required; >300 grams (~2/3 lb) of sample less than 420μm required if testing metal dusts]
- Go/No-Go Screening + Combustible Dust Screening Package - Both tests run in tandem as a screening package
- Sample Characterization Test - includes determining the sample moisture content and particle size distribution [>30 grams of samples less than 420μm required]
- “Hard-to-ignite” Explosibility Test - Tested as above but with a 400 J ignition source. [>100 grams (~¼ lb) of sample less than 420μm required]
Unless otherwise instructed, dust testing is performed on the sample as it is received (“as received”) from your facility as mentioned earlier. It may be screened to less than 420 μm (40 mesh) – OSHA’s and NFPA’s demarcation of a “dust” – to facilitate dispersion into a dust cloud. Particle size may vary widely depending on the sample.
Furthermore, please note that per ASTM recommendations (and some NPFA requirements); samples should be tested at a particle size less than 75 μm and less than 5% moisture. Please note that testing materials in a method not complying with the ASTM/EU recommendations may produce explosion severity and explosion sensitivity data that is not considered conservative enough for explosion mitigation design.
On-Site Dust Hazard Assessments (DHA)
FAI combustible dust experts can visit your facility to evaluate your receiving, storage, use, processing and disposal of all “powder” materials. They will evaluate existing dust management programs, handling practices, equipment, fire/explosion suppression systems, warning devices and onsite extinguishing capabilities. Possibilities for fugitive dust control will also be identified where appropriate. FAI can provide the following services:
- Incident investigation for dust explosions and fires
- Evaluate compliance with relevant national, local and industry standards
- Electrostatic hazards – e.g. grounding and bonding issues
- Recommendations for explosion hazard risk reduction
- Identify dust sampling points and collect samples for dust explosibility testing
NFPA and OSHA NEP Combustible Dust Compliance
- Preparation for an OSHA Combustible Dust NEP inspection, including appropriate responses to inspector’s questions
- Perform a Process Hazard Analysis (PHA) for compliance with NFPA
- Documentation review for NFPA and OSHA Combustible Dust NEP requirements
- Testing services to meet all NFPA and OSHA Combustible Dust NEP requirements
- Conduct employee training to comply with OSHA Combustible Dust NEP requirements
Additional Services
- Vent size calculations for new or existing equipment (American and European standards)
- Ignition source evaluation (NFPA 654 and 77)
- Electrical area equipment classification (NFPA 499)
- Integration of combustible dust hazard management into existing process safety programs for process safety management (PSM) facilities
- Development of process safety programs to manage combustible dust hazards for non-PSM facilities
Electrostatic Hazards
Identifying the electrostatic characteristics of a material is an important step when evaluating the hazards associated with a process, especially for those that handle materials that exhibit low ignition energies.Charge separation and accumulation are inherent problems resulting from industrial operations that handle powders of low conductivity. This charge separation and accumulation is a product of the friction and impact between particles that occurs during the movement of granular material during a variety of typical process operations.To identify potential static electrical hazards of a material, it is important to evaluate the level of charge separation and accumulation that occurs during transport, the resistivity of the material and how quickly any accumulated charge can be dissipated.
Materials we refer to here include all types of flammable hazards including combustible dust/dust hazards, flammable liquid, flammable gas and flammable vapors. The prevention of dust explosions and other fire hazards are are the basis of comprehensive process safety management programs. Necessary combustible dust testing, liquid flammability testing
Streaming current is defined as the current generated from the flow of charged materials. The level of streaming current generated depends upon the static electricity characteristics of the material and the nature of the process. Unfortunately, there is no relationship between the streaming current in powders and that of liquids (1). In these instances, experimental determinations must be made to identify ignition hazards that may result from charge accumulation during process operations. From these types of
1 R.A. Mancini, “The Use (and Misuse) of Bonding for Control of Static Ignition Hazards, “Plant/Operations Progress (Jan.1998) 7(1): 24.
To identify the streaming current and charge accumulation of a material, Fauske & Associates (FAI) provides a Powder
To further classify the powder, it is necessary to evaluate the resistivity of the material. This is done per ASTM D257. The resistivity of a powder is governed by the particle size, level of surface contamination and packing density of the material and often is quite different than the resistivity of the material in its pure solid form. Powders with high resistivities typically lose their charge very slowly, even when the process equipment is properly grounded. In some instances, this can translate to poor heat dissipation and can lead to potential fires (2). More importantly, improper handling of materials with both high and low resistivity can create hazardous scenarios. Insufficient grounding and bonding of process equipment can lead to high levels of charge accumulation. At some point, a threshold is reached and charge breakdown occurs resulting in
At FAI, we follow ASTM D257 to evaluate the volume and surface resistivity of a material. The volume resistivity can be determined by measuring the electrical resistance between opposite faces of a volume of powder. The volume resistivity of the material, commonly expressed in ohm-meter, can then be used to classify the material as either a conductive, dissipative or insulative. Likewise, the surface resistivity can be characterized by slightly modifying the test procedure. The units for surface resistivity are ohms per square. The square refers to any square geometry of a material, whether it be a square meter, square foot or square centimeter. The ranges used to characterize a material based on these parameters are shown below.
Results from a resistivity test conducted on a Pittsburgh pulverized coal sample using this method are shown below.
Another important electrostatic characteristic is the charge relaxation time of powders. This property varies greatly amongst different materials and is hard to estimate even if the dielectric constant of the material is approximated because it does not follow the hyperbolic trend found in liquids. The proper method to evaluate the charge decay time of a specific powder is to directly measure it. Once an understanding of the time required for a charge to relax for a given powder is gained, process parameters such as
At FAI, a JCI 155 Charge Decay Test Unit is used to measure the charge decay of powders. This piece of equipment is programmed to apply a
From the tests conducted on Pittsburgh pulverized coal, it can be seen that the material is very resistive in powder form. Processing this material will likely result in charge accumulation and could reach conditions that result in a hazardous static electricity discharge. However, by utilizing this data, it is possible to minimize this risk by implementing proper grounding and bonding of process equipment. The data also provides clues on how to adjust process parameters to reduce charge
Gaining an understanding of the electrostatic characteristics of a particular material can greatly assist in the assessment and mitigation of fire and explosion hazards in the process environment. For additional information on assessing electrostatic hazards, please contact FAI at dust@fauske.com or 630-323-8750.
References
Pratt, Thomas H. Electrostatic Ignitions of Fires and Explosions. New
Britton, Laurence G. Avoiding Static Ignition Hazards in Chemical Operations
Training
Our team is happy to help train your staff in the understanding of technical issues, process safety programs or audits, regulations and more. We perform process safety audits as part of a comprehensive hazards analysis and can work with you to make sure your staff is supplied with skills training needs in many ways including:
Level I - Gap Analysis
Level II - Training & Consulting
Level III - Program Development and Implementation
Partial List of Services Offered:
- Reviews and upgrades of all your safety process systems and regulatory requirements
- VPP Consulting
- Audits, reviews, and upgrades of all your Operating, Safety, and Maintenance Procedures
- Training program evaluations for both completeness and effectiveness (from technical skills to professional development) and upgrades where needed
- Reviews and upgrades of your program elements such as Employee Participation and Process Safety Information for effectiveness and completeness
- Work process effectiveness evaluations and upgrades
- Overall organizational development (e.g., motivation, work processes)
- Stress reduction
- Evaluations of the effectiveness of communication
We design, custom develop and deliver any site specific training materials needed by your organization. Our Consultants, Engineers and Technical Specialists are available to deliver the classroom, lab or on-the-job training your staff needs. In addition, we will assist with the identification and procurement of commercially available training materials where available.