Effects of Temperature on LOC of Dimethyl Sulfuxide Mixed With Higher Vapor Pressure Solvent
By: T.J. Frawley, Flammability Project and Lab Manager, Fauske & Associates
Dimethyl Sulfoxide (DMSO) is an extremely versatile solvent with uses spread across multiple industries. It is a by-product of the wood industry, has many uses in the medical field (although some uses are controversial), is an effective solvent due its high solubility, and can be used as a reaction solvent in manufacturing (DMSO.com).
DMSO’s effectiveness is partially due to the relatively nonvolatile nature of the substance when compared to other solvents. It has a high boiling point of 189°C and a low vapor pressure. The vapors are quite dense, with a vapor density of 2.70. Air has a vapor density of 1.0. The combination of dense vapors and low vapor pressure contribute to its, again, relatively high flash point temperature of 87°C.
From a process safety standpoint, as long as the process is ran below the 87°C with DMSO alone, there is little risk. However, once another solvent with a lower flash point is mixed with DMSO, the flash point of that mixture will drop below 87°C, creating an explosive environment. If the process requires higher temperatures and high pressures, the danger increases with additional each degree and millibar.
If you are reading this, I feel safe in assuming that you are aware of the fire triangle and the hazards that exist working with the boundaries of that three-corners geometric shape of fire and fury. Before you think to mitigate the hazard through vent sizing or any other method, let us discuss prevention.
Your product is fuel. Cannot eliminate that leg of the triangle. And while you can attempt to reduce the exposure of your process to an ignition source, it is near impossible to eliminate every single, minute, possible, feasible, conceptual, source of ignition.
This leaves our final leg of the triangle, Oxygen. Here is where the Limiting Oxygen Concentration (LOC) test comes into play. If the process is anaerobic, you can completely inert your process with Nitrogen or Argon. This can get expensive as Nitrogen is not cheap, Argon less so. So you perform an LOC test to determine the lowest percentage of oxygen needed to sustain flammable propagation. And you run your process beneath that number. You are now on the off ramp exiting the danger zone.
But engineer beware. As the temperature increases, the amount of Oxygen needed to propagate an ignition decreases.
Assuming at 1:1 ratio mixture by volume of DMSO and another solvent with a flash point lower DMSO, the LOC of the mixture will decrease as the temperature increases. At lower temperatures the partial pressure of the mixture’s vapors will consist mostly of the other solvent. Not enough of the DMSO has vaporized to propagate an ignition in environments that are starved of oxygen. For example, say Sample A has an LOC of 10% O2 at 14.7 psia at 100°C and DMSO has an LOC of 6.5% O2 at 14.7 psia at 100°C. The LOC of the mixture of Sample A and DMSO will be closer to 10% O2 because the partial pressure will consist of a greater percentage of the less dense vapors of Sample A.
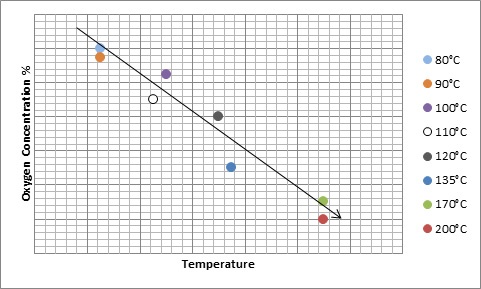
However, as the temperature increases, so too does the vapor pressure of the DMSO. Thus, the partial pressure of the vapor is comprised more of DMSO molecules. The LOC of the mixture will begin to drastically decrease, moving away from the LOC of Sample A and beginning to reflect an LOC closer to that of DMSO.
The moral of the story is to beware when working with DMSO within a process. It is a very useful and diverse product that spans industries. The presence of DMSO drastically lowers the LOC of a mixture as temperatures increase.
For more information on FAI flammability services, contact T.J. Frawley at 630-887-5289 or frawley@fauske.com. www.fauske.com