What is DIERS Design Institute for Emergency Relief Systems?
Under the AIChE “The Design Institute for Emergency Relief Systems (DIERS) was formed in 1976 as a consortium of 29 companies to develop methods for the design of emergency relief systems to handle runaway reactions
DIERS SPENT $1.6 million to investigate the two-phase vapor-liquid onset/disengagement dynamics and the hydrodynamics of emergency relief systems. Of particular interest to DIERS were the prediction of two-phase flow venting and the applicability of various sizing methods for two-phase vapor-liquid flashing flow.
DIERS became a Users Group in 1985 with over 200 companies (75 percent domestic and 25 percent international) ultimately requesting membership and having their corporate representatives participate in the semi-annual meetings.
table of Contents
The Purpose of DIERS
- To reduce the frequency, severity, and consequences of pressure producing accidents, and
- To develop new techniques which will improve the design of emergency relief systems.
Fauske & Associates (FAI) was the principal research contractor for the Design Institute for Emergency Relief Systems (DIERS), an extensive R & D program sponsored by those 29 companies under the auspices of AIChE and completed in 1985. Company founder, Dr. Hans K. Fauske served as the principal investigator and overall technical leader of the DIERS research project. A primary purpose of that effort was the evaluation of emergency relief vent requirements, including energy and gas release rates for systems under upset conditions and the effect of two-phase flow on the emergency discharge process.
The DIERS program resulted in the development of a bench-scale low thermal inertia adiabatic calorimeter, which was first commercialized as the Vent Sizing Package (VSP2™). Later improvements led to the VSP2™. The Reactive System Screening Tool (RSST™) was introduced by FAI in 1989 to provide an easy, inexpensive approach to the DIERS testing method. Recent enhancements led to the Advanced RSST (ARSST™) in 1999. FAI uses the DIERS-based VSP2™ and ARSST™ calorimeters to characterize chemical systems and design emergency pressure relief systems. Both instruments provide vent sizing data that are directly applicable to the process scale.
Dr. Fauske provided overall technical direction for the AIChE’s acclaimed DIERS program formed to develop methods for the design of emergency relief systems to handle runaway reactions. Currently, Dr. Fauske is performing a pivotal role in resolving potential process safety issues and the development of inherently safe nuclear and chemical process reactor concepts.
Technical Background
Published in 1986 by Elsevier Thermochimica Acta, “Thermal Runaway Reactions In a Low Thermal Inertia Apparatus” by Dr. J.C. Leung and Dr. H.K. Fauske of Fauske & Associates along with Dr. Harold Fisher of Union Carbide Corporation, as shown below states: "A new apparatus utilizing a unique low heat capacity sample container is described for studying thermal runaway reactions. Other features provided by this new technique include nearly equal pressures between the sample container and the outside containment vessel as the runaway proceeds, a nearly zero temperature gradient outside the sample container to minimize heat loss, a magnetic stirring mechanism, and a remote feed capability. Thermal data obtained for styrene polymerization and di-t-butyl peroxide decomposition were shown to be in excellent agreement with previously published kinetic models. Finally, a base-catalyzed phenol-formaldehyde reaction in a runaway situation is presented." Here, in the intro, two devices commonly used to obtain information on the exothermicity of runaway reaction are the differential scanning calorimeter (DSC) and the accelerating rate calorimeter (ARC) are introduced.
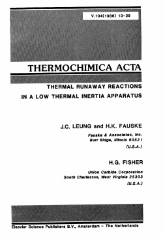
In the April 1987 Plant/Operations Progress issue,
Dr.'s Joseph C. Leung and Fauske of Fauske & Associates extended the applications further in "Runaway Systems Characterization and Vent Sizing Based on DIERS Methodology." Looking beyond trends, the article discusses the diverse nature of runaway systems. Vent sizing for 50 industrial chemical systems testing over 2 years. Please see more here:
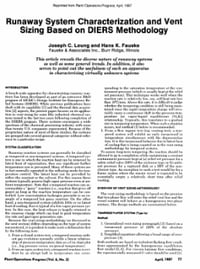
Published in Plant /Operations Progress (July 1988)
Dr. Fauske wrote: Emergency Relief System Design for Reactive and Non-Reactive Systems: Extension of the DIERS Methodology."In it, he states: "Simple mechanistic models for reactive and non-reactive chemicals are summarized. The DIERS methodology has been extended as well as simplified to account for vapor disengagement and frictional effects, including laminar flow conditions-both principal objectives of the DIERS program." He further points out that while two-phase flow phenomena in connection with relief system design for runaway chemical reactions were recognized in past research and computerized modeling by Boyle and Huff, a database is seldom available due to provide vent sizing due to the need for extensive thermokinetic and thermophysical characterizations of the reacting systems. Thus, less complicated analytical methods allowing vent sizing from direct test data such as the DIERS bench-scale apparatus is preferred. For the first time, runaway reactions in the DIERS can approximate the severity of those in industrial vessels. "the simplified models together with the bench-scale equipment is now commercially available under the trademark VSP (Vent Sizing Package)…"
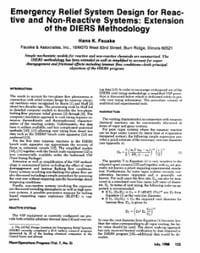
In 1990, “An Easy, Inexpensive Approach to the DIERS Procedure”
“An Easy, Inexpensive Approach to the DIERS Procedure,” Michael J. Creed and Dr. Fauske, both of Fauske & Associates published the article below stating, "The DIERS program included two key contributions. One was emphasizing the importance of correctly determining the source term energy-release and gas-generation rates for vapor and gassy systems, respectively) under upset conditions and the development of a new bench-scale apparatus with which such a determination can be obtained and extrapolated directly to full-scale application. The other was emphasizing the importance of two-phase flow in the emergency-relief discharge process and the development of vent-sizing techniques that are valid for multiphase behavior.
It has been suggested, however, that the DIERS methodology can be so complex and time consuming that it may be beyond the capability of the small facility operator and, therefore, hat much more user-friendly techniques must be developed. Hopefully, the inexpensive and easy-to-use methodology summarized here will satisfy this need and encourage the widespread use of the AIChE-IDERS vent-sizing methodology.”
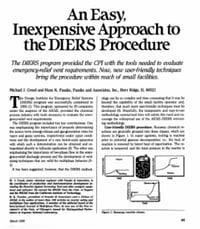
Many white papers, articles, and blogs have been written by Fauske & Associates since 1980 about relief system design, runaway reactions, the ARSST™, the VSP2™, DIERS, two-phase flow and more. Here are a few:
- Advanced Reactive System Screening Tool (ARSST™)
- A model of the Dilution of a Forced Two-Phase Chemical Plume in a Horizontal Wind
- A Practical Approach to Capacity Certification
- ARSST™ Experiments to Evaluate Solvent Compatibility with Stabilized Lithium Metal Power
- Determination of Two-Phase Flow Regimes and Pressure Relief Sizing
- Emergency Relief System Design for Reactive and Non-Reactive Systems: Extension of the DIERS Methodology
In the Winter 2019 Issue of FAI’s Process Safety News, Dr. Fauske teased “Clarification of Non-Equilibrium and Equilibrium Flashing Flows: A simple and easy to apply two-phase flow model that is in excellent agreement with safety valve, and nozzle-tube data is illustrated below. The constant flow area length L is the key parameter and values leading to non-equilibrium (short) and equilibrium (long) flashing flows are provided by the flow model. The nozzle inlet condition can be a subcooled liquid, a saturated liquid or low quality two-phase vapor-liquid mixture, all conditions predicted accurately by the simple flow model. The details and simple model example calculations will be presented at the AIChE DIERS September 16-18, 2019 meeting in Burr Ridge, Illinois, by Hans K. Fauske, D.Sc. Emeritus President and Regent Advisor, Fauske & Associates.”
Relief System Design Training
Fauske & Associates proudly provides training and regularly published articles and blogs on these topics. The popular Relief System Design Course provides CEUs and is generally taught over two days.
Unlike other emergency vent sizing course, this curriculum highlight simplified calculation methods capable of giving safe – but not overly conservative relief system designs, with an emphasis on reactive chemistries and the role of two-phase flow.
Benchmarking of these methods will be illustrated with incidents and available plant data. Utilization of methods and equations is demonstrated through practical design examples, covering vapor, gassy, and hybrid systems.
Attendees will participate in group workshops and complete an independent quiz at the end of the course to ensure comprehension of the material. A laboratory session demonstration of experimental techniques is included.
Course Topics – Day 1
- Introduction to Vent Sizing and Case Study
- Vent Sizing Fundamentals
- Codes and Standards Explanation
- History for DIERS
- Tow-Phase Flow Considerations
- Experimental Considerations
- Vent Sizing Based on All Gas or Vapor Venting

Course Topics – Day 2
- Vapor System Vent Sizing
- Gassy System Vent Sizing
- Hybrid System Vents Sizing
- Simplified Two-Phase Flow Methods for Vapor, Hybrid and Gassy Systems
- Non-Reactive Fire Sizing

Course Topics – Day 3
- Stable Relief valve Operation
- Discharge Coefficient Evaluation
- Containment and Disposal Considerations
- Lab Demonstrations

Learning Outcomes
- Understand up-to-date DIERS vent sizing methodologies and models, as well as the role of single and two-phase flow in venting behavior
- Perform vent sizing calculations using the correct models and methodologies
- Apply adiabatic calorimetry data
- Be able to use hands-on techniques and “rules of thumb” to ensure that realistic vessel and vent size conditions are specified
contact FAIUniversity@fauske.com or click here:

More On the ARSST™ and VSP2™
Advanced Reactive System Screening Tool™ (ARSST™) Background
Fauske & Associates' (FAI) Advanced Reactive System Screening Tool™ (ARSSTTM) is a low thermal inertia calorimeter used to obtain critical upset process design data. FAI offers the ARSST™ along with options for customization such as a high-pressure vessel and flow regime detector, as well as commonly used items such as test cells, heaters, glands, and thermocouples. At FAI, we not only utilize the ARSSTTM in our fully equipped hazards laboratory, but we also manufacture and sell the calorimeter for use by our clients.
The ARSST™ is based on DIERS two-phase methodology, which is recognized by OSHA as an example of good engineering practice. This easy-to-use device is also capable of generating low phi-factor data for DIERS vent sizing and is an excellent tool for industry as well as any university engineering lab for research or unit operation studies.
ARSST™ tests are used to model such upset scenarios as loss of cooling, loss of stirring, mischarge of reagents, mass-loaded upset, batch contamination, and fire exposure heating. This easy to use and cost-effective calorimeter can quickly and safely identify potential reactive chemical hazards in the process industry. ARSSTTM data yields critical experimental knowledge of the rates of temperature and pressure rise during a runaway reaction, thereby providing reliable energy and gas release rates which can be applied directly to full-scale process conditions.
The ARSST™ typically utilizes a sample size of 5-10 grams in a lightweight glass test cell with a volume of approximately 10 ml. The test cell is outfitted with a belt heater (used to heat the sample through a preprogrammed temperature scan) and then installed in 350 ml containment vessel. Tests are typically run using open test cell methodology. In this test configuration, the test cell is vented to the containment vessel. Volatilization of the test sample is prevented by imposing inert backpressure on the containment vessel.
Benefits
The ARSST™ enables users to quickly obtain reliable adiabatic data which can be used for a variety of safety applications including characterization of material compatibility, thermal stability, and reaction chemistry. Test data includes adiabatic rates of temperature and pressure change which, due to the low thermal inertia, can be directly applied to process scale to determine relief vent sizes, quench tank designs and other relief system design parameters related to process safety management.
Features
- User-friendly
- Easy setup for fast test turnaround
- Quickly screen new and existing processes for thermal hazards
- Scanning and isothermal modes
- Reliable results for thermal hazard assessment
- Open or closed cell testing (obtain vapor pressure data from closed cell testing)
- Small sample size
- Lightweight glass test cell with proper mixing
- Compatible with Flow Regime Detector (FRED) equipment for vent sizing applications (FRED distinguishes between foamy and non-foamy behavior)
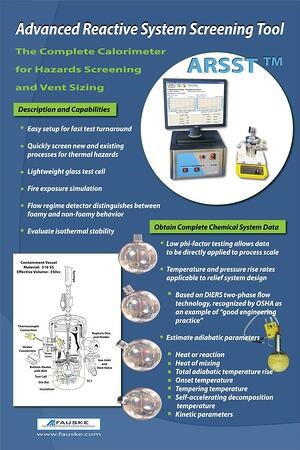
Applications
- Obtain complete chemical systems data:
- Critical temperature
- Kinetic parameters
- Vent sizing
- Emergency relief system design
- Accommodates handling of energetics and pyrotechnics
- Estimate process safety parameters, including:
- Onset temperature
- Temperature & pressure rise rates
- Adiabatic temperature rise
- Heat of reaction and mixing
- Tempering temperature
- Time to maximum rate (tmr)
- Self-accelerating decomposition temperature (SADT)
Vent Sizing Package 2 (VSP2™) Background
Fauske & Associates' (FAI) Vent Sizing Package 2™ (VSP2™) is a low thermal inertia adiabatic calorimeter used for process hazard characterization that utilizes state-of-the-art DIERS technology to obtain critical upset process design data. It is the commercial version of the original DIERS bench-scale apparatus. At FAI, we not only utilize the VSP2™ in our fully equipped hazards laboratory, but we also manufacture and sell the calorimeter for use by our clients.
Its versatile and innovative design allows the VSP2™ to simulate upset (abnormal) conditions which might lead to a runaway chemical reaction (e.g., loss of cooling, loss of stirring, mischarge of reagents, mass-loaded upset, batch contamination, fire exposure heating, etc.). Resulting temperature and pressure rise rates are directly scalable since it is a low thermal inertia (phi-factor) apparatus.

Benefits
The VSP2™ utilizes established DIERS technology to identify and quantify process safety hazards so they can be prevented or accommodated by process design.
Test data includes adiabatic rates of temperature and pressure change which, due to the low thermal inertia, can be directly applied to process scale to determine relief vent sizes, quench tank designs and other relief system design parameters related to process safety management. Adiabatic data obtained with the VSP2™ can be used to characterize reactive chemical and consequences that could occur due to process upset conditions.
Features
The versatile configurations offered by the VSP2™ design directly simulate process conditions including:
- Loss of cooling or agitation
- Accumulation or mischarge of reactants
- Contamination of batch
- Thermally initiated decomposition
- Resident incubation time
- In-situ liquid/gas dosing or sampling
Applications
Use of the VSP2™ can help users obtain complete chemical system data such as:
- Low thermal inertia testing allows data to be directly applied to process scale
- Temperature and pressure rise rates applicable to relief system design "Based on DIERS two-phase flow technology, recognized by OSHA as an example of “good engineering practice”
- Many testing configurations
- Many testing configurations
- Closed or open (vented) tests
- Scaled blowdown simulation
- Test cells are available in 304 & 316 SS, Hastelloy C, Titanium and glass
- Accurate adiabatic data
- Onset temperature
- Total adiabatic temperature rise (ΔTad)
- Heat of reaction or mixing
- Vapor pressure data
- Time to maximum rate (tmr)
- Self-accelerating decomposition temperature (SADT)
- Relief valve sizing
- Quench tank design
- Effluent handling
- Critical temperature
- Effect of two-phase flow

FAI has also created the FERST software to allow users to implement practical emergency vent sizing using industry-recognized methodology. It applies DIERS methodology (including the Leung-Omega and Fauske methods) for reactive chemistry and API 520/2000 or NFPA 30 for non-reactive systems.
Gabe Wood, Manager of Thermal Hazards Testing & Consulting at FAI, recently presented "Using the VSP2™ to Perform Relief Sizing on Epichlorohydrin Chemistry” to the DIERS User Group Meeting in Germany. Here is a video as he explains the presentation to us: