Process Safety Hazard Identification: A Scale-Dependent Approach
By Elizabeth Raines, Senior Chemical Engineer at Fauske & Associates, eraines@fauske.com
Introduction
Evaluating chemical hazards is a crucial part of plant safety. Any chemical process should be robust by design; any given process can be subject to reasonable changes. A robust design should accommodate small changes without a catastrophic consequence. To develop an inherently safe process, hazards need to be identified and evaluated in order to either prevent, mitigate, or eliminate them.
Reactive chemical hazards can be present whether the reaction is intended or not. It is essential to consider the presence of hazards throughout the various developmental stages or scale of production. This article provides recommendations for consideration at any step in production: from discovery to commercialization. It is important to note that every process is different. The level of detail spent analyzing any given parameter needs to be commensurate with the level of risk and hazard level.
Discovery & Early Development
Goal: Identify target material and start development of a synthetic route for manufacturing
Scale: Typically, on the lab scale up to potentially pilot or kilo plant scale
When a new chemical (or new to your facility) is targeted for production, the first critical step for developing an inherently safe process is identifying primary chemical hazards. This step in the process typically involves a combination of desktop screening and small-scale testing. It is crucial to identify glaring reactive hazards to ensure production is feasible. Examples of critical parameters that should be considered when developing a safe process are listed in Table 1.
Table 1 – Key Components for Hazard Assessment
At the discovery stage of a project, it is crucial to identify any compounds or intermediates that possess explosive properties and recognize the burden that would place on lab and/or further scale-up production.
Desktop Screening
The first step in identifying chemical hazards involves literature searches and theoretical estimations. It is advisable to start by listing all relevant process materials (e.g., raw materials, intermediates, products, catalysts, solvents, by-products, off-gases). Once the key components have been identified, it is recommended to review available information and identify gaps in knowledge compared to the critical hazard assessment parameters listed in Table 1. A few critical steps for this exercise:
- Collect and analyze SDS for involved components to identify any listed hazards (e.g., flammability or toxicity concerns).
- Evaluate the active components' chemical structures to identify known reactive, toxic, or energetic functional groups (e.g., halogenated components, azides, picrates, nitro compounds, peroxides or peroxide formers, metal hydrides, low-molecular-weight alkynes, etc. See Bretherick’s Explosive Group Table).
- Review reputable sources to identify essential material properties, known hazards, or past incidents with active or similar components (some familiar sources include Bretherick’s Handbook of Reactive Chemical Hazards, NFPA 491: Guide for Hazardous Chemical Reactions, Sax & Lewis, CCPS PSID database, WISER, etc.).
- Research available information on the heat of reaction, kinetics, or any information on known decomposition reactions. If none are available, it is advisable to determine the theoretical heat of the reaction, if possible.
- Assess if the product can be transported or if there are any known restrictions.
- Identify any unique storage requirements.
- Ensure all materials can be handled by the facilities Emergency Response Plan; identify any gaps.
Small-Scale Testing
After the apparent hazards have been identified through the desktop search, small-scale testing can be employed to fill the gaps in the hazard assessment and aid in developing the synthetic pathway and reaction parameters. Small-scale testing is a critical component of creating a basis of safety before moving to larger‑scale production. This crucial information can then be carried throughout the development of the material to ensure safety at any scale.
At this testing phase, the first essential steps involve ensuring the use of appropriate PPE (as determined by identifying the potential toxicity hazards during the desktop screening) and confirming that flammability and explosion hazards are known and protected against. If these potentially hazardous parameters are unknown, experiments should be performed to characterize them. Examples of essential parameters at this stage include shock sensitivity, explosion propagation, or others that can affect required handling procedures even at a small-scale.
Besides determining fundamental material properties, this is a sound stage of production to evaluate the involved materials' thermal properties and better understand the thermal behavior of the desired reaction. Thermally screening (e.g., DSC or TGA experiments) starting materials, intermediates, and products can help identify the magnitude of the heat of reaction or decomposition. This can provide an indication of thermal stability for the various components and help identify primary hazards to analyze in more detail. Performing small‑scale testing during the development stage can also help guide the selected reaction conditions. Some considerations during this exercise are:
- What are the required steps to make the product?
- What type of conditions (e.g., temperature or pressure) are required to make the right product?
- What are the heat of reaction, adiabatic temperature rise, and expected gas evolution during the desired process?
- Given the reaction behavior, identify the optimal processing method (e.g., batch, semi-batch, continuous, reflux, etc.).
- Are there solvent-reagent interactions?
Overall, the purpose of this stage in the lifecycle of chemical production is to ensure key hazards are identified prior to handling the process at an appreciable scale, and that the process and materials involved do not entail conditions that would make scale-up or production impractical.
Scale-Up
Goal: Develop a process that will safely produce a product on a commercial scale that accounts for the differences in physical and chemical phenomena per scale
When a material has been selected and is headed for commercialization, and no significant hazards have been identified that would eliminate production feasibility, the scale-up process begins. At this step in the process, it is essential to fully characterize the thermal stability of the components identified as potential thermal hazards during discovery/development, quantify the desired reaction in the way it is intended to be performed, perform a detailed hazard assessment considering the planned production procedure and available production equipment, and quantify potential adverse reactions.
Thermal Stability Evaluations
Depending on the results of the thermal screening experiments conducted during the discovery/development stage, a detailed thermal stability evaluation may be necessary to ensure that the selected process conditions are appropriate. Common types of experiments designed to evaluate thermal stability include the ARSST, VSP2, ARC, DSC, or the TAM. Key parameters that can help evaluate the thermal stability for process scale‑up include the adiabatic time to the maximum rate (TMR) or the self‑accelerating decomposition temperature (SADT). These evaluations can also be used to extract temperature‑dependent kinetic information that can be used to perform simulations of various processing or upset scenarios to determine conditions to avoid or their consequences. This evaluation is also essential at the commercialization scale.
Quantification of the Desired Reaction(s)
The development stage provided recommendations on how the synthesis of the desired product should be performed. The detailed thermal stability evaluation will indicate what is practical from a safety standpoint. Together with the information collected during the preliminary hazard assessment, a potential plant procedure can be prepared. To ensure that plant equipment can adequately handle the desired reaction with the desired procedure, reaction calorimetry can simulate the process. Reaction calorimeters such as the Mettler Toledo RC1 or Chemisens CPA202 can be used to simulate the process and collect crucial information. Critical parameters such as instantaneous heat flow, heat of reaction, heat capacity, and noncondensable gas generation rate can be determined. These parameters are vital in determining if process equipment provides sufficient cooling capacity (i.e., is there a balance between the heat generation from the reaction and the vessel's heat removal capabilities) or scrubbing capacity. If not, adjustments to the procedures can be made until there is confidence that the process can be safely performed at a large scale.
Detailed Hazard Assessment
Now that a procedure and process equipment have been identified, a more detailed process hazard assessment (PHA) can be performed. A PHA is a systematic evaluation of hazards and is required for initiation of a process and periodically after that. A PHA's goal is to identify hazards during normal operating conditions (e.g. start-up, shut down, and steady-state operation) and abnormal conditions (e.g., emergency or upset situations). The ultimate goal of the PHA is to identify hazards that are likely (in terms of ease or frequency) and considered severe (in terms of consequences) to determine gaps in controls, procedures, equipment, or others. If unacceptable risks are identified in the regular operation, it may be necessary to revisit the desired reaction's hazard quantification. Standard tools for facilitating a PHA include:
- Hazard and Operability Studies (HAZOP)
- “What-if” analysis
- Failure modes and effect analysis (FMEA)
- Checklist analysis
- Fault tree analysis
- Batch Sheet Review (operating procedures) for the process under consideration.
Quantification of the Undesired Reaction(s)
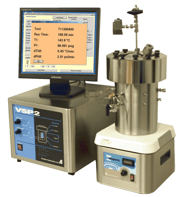
It can be challenging to predict the outcome of a hazard identified during a PHA. Still, it is crucial to evaluate the consequences to ensure either prevention, mitigation, or elimination of the hazard. A common potential hazard in a chemical process is an undesired chemical reaction not accounted for when planning the process, procedure, or equipment. Examples of upset scenarios that can lead to an undesired reaction or reaction rate include Incorrect Reactants, Impurities, Corrosion by Reactants, Too Much/Little Reactant or Solvent; Reactant Added Fast/Slow, Fire Exposure, Vacuum Failure, Water or Air Intrusion, Agitator Failure, etc. Low phi-factor (low thermal inertia) adiabatic calorimeters such as the VSP2 or ARSST can be used to directly simulate these upset scenarios to understand the severity of the hazard. The information collected during these experiments is directly scalable to full-sized vessels. The data can be used to design or evaluate relief devices such as rupture discs or pressure relief valves using software programs such as FERST powered by CHEMCAD. The information is also crucial for developing effluent handling systems or understanding when an upset scenario or hazard needs to be eliminated by a procedure or equipment change.
The scale-up stage's goal is to provide a thorough basis of safety where detailed process, procedure, and equipment evaluations have been conducted to ensure the safety of the workers, community, and environment.
Commercialization
Goal: Conduct processing at the full manufacturing scale, and evaluate safe storage and transportation conditions
Scale: Typically on the pilot or kilo plant scale through the manufacturing scale
Now that the chemical hazards have been identified and then either mitigated, eliminated, or prevented (by procedure or equipment changes) the process is ready for commercialization. Maintaining a safe manufacturing process is completed by providing and maintaining the correct level of engineering controls, proper working practices, and adequate personal protective equipment. This also involves creating good (i.e., simple to understand) plant operating procedures, providing thorough operator training, and managing change. Further, it is essential to revisit the PHA exercise periodically to ensure that new hazards are not introduced and that the best practices available remain in use. Other considerations during this stage include:
- Review any changes to the process or equipment
- Document any changes in addition to the safety review of the changes
- Confirm that the safety review procedure has been followed and was effective
- Institute any changes to procedures to streamline or make the process more effective
As far as identifying safe storage and appropriate transportation conditions, the evaluations conducted during the earlier stages of the chemical process development can provide a basis for these recommendations. The thermal stability evaluations can help identify the temperature dependency of any unwanted reactions. That information can be combined with predicted package-specific heat removal capabilities to ensure the storage conditions are innocuous. Similarly, the completed hazard assessments can ensure that an appropriate hazard classification is selected per the UN Model Regulations to ensure safe transportation.
The commercialization stage's goal is to strive for continuous improvement while maintaining safety during operation, storage, and transportation by periodically reviewing the completed hazard assessments.
Resources
- www.fauske.com
- Hendershot, D. C., “A Checklist for Inherently Safer Chemical Reaction Process Design and Operation,” Center for Chemical Process Safety International Conference and Workshop on Risk and Reliability, 2002.
- Barton, J. and Rogers, R., “Chemical Reaction Hazards,” Second edition, Gulf Publishing, 1997.
- Bretherick, L., “Bretherick’s Handbook of Reactive Chemical Hazards,” Seventh edition, Butterworth Heinemann, 2008.
- Stoessel, F., “ Thermal Safety of Chemical Processes: Risk Assessment and Process Design,” Wiley‑VCH, 2008.
- Weisenburger et al., "Determination of Reaction Heat: A Comparison of Measurement and Estimation Techniques," Organic Process Research and Development, 2007, 11, 1112-1125.