Revisiting Mitigation Options for Acoustic Resonances in Pipe Attachments
By Jens Conzen, Director of Plant Services, Fauske & Associates
Typical power and process plant systems will always vibrate under operation to some degree. This is due to various reasons such as turbulence, acoustics, or excitation from rotating equipment, for example. Acoustic resonance in piping systems can be caused if dead ended side branches, stand pipes, or drip legs are being excited. The flow across the throat of the attachment can produce a vortex shed on the leading edge of the entrance that occurs at a constant frequency. If that frequency is close to the quarter wave length frequency of the branch, an acoustic resonance can occur as exemplified in the graphic below:
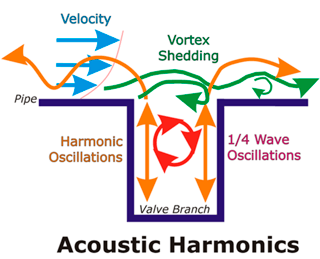
In this case, one would refer to the event as flow-induced vibration. The natural frequencies for the various geometries can be estimated by using simple algebraic formulations. The frequency of vortex shedding can be estimated by following the guidance of Ziada and Shine [1]. If vibration data taken with accelerometers and strain gauges suggest an acoustic resonance at unacceptable levels (see also FAI N-16-13), and it is also confirmed by acoustic screening calculations, actions must be taken for mitigation.
A variety of options (operational and hardware changes) exist that can help mitigating the vibration amplitude for side branch excitation.
Plant Operation:
For partial load operation, it might be possible to close one process line and consequently increase the flow velocity in the remaining lines. This could decouple the excitation source. However, this should be carefully verified by analysis and testing.
Plant Modification:
The main options for pipe line modifications are: 1) a vesselet configuration to decouple the vortex shedding frequency from the cavities, 2) an acoustic side branch to add damping and disturbance, or 3) an open bypass connection to add disturbances. Schematics for these options are shown below.
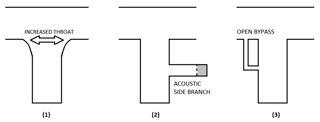
A vesselet inlet configuration increases the throat width which causes the frequency of the vortex shed to change. In addition, the edges of the inlet to the drain stub are rounded with a fairly large radius compared to a sharp edge. This measure makes it more difficult for a distinct vortex shed to establish at the leading edge. A vesselet configuration would most likely decouple the excitation from the cavity. Vesselet branch connections have been used in industry application (see photo below).
An acoustic side branch (ASB) may be installed to mitigate the resonance phenomenon. This concept has also been proven successful in the industry. The ASB changes the frequency of the attachment and it contains a material that dampens the acoustic pressure. The acoustic pressure loading may not be eliminated with an ABS, but appreciable reductions in amplitude and shift in frequencies have been observed.
An open bypass adds disturbance to the cavity that could disrupt and lift the quarter wave. This has been tested for drip legs; opening of the drain valve at the bottom of the drip leg eliminates the vibration. The flow through the bypass “stirs” the cavity, which makes it difficult for a quarter wave to develop. However, this solution is only effective if there is continuous flow through the bypass. This can only be achieved by adding resistance into the main line.
Other potential solutions may include changing the length of the attachments or by adding a spoiler just upstream on the leading edge of the tee connection (see photo below).
In any case, it is recommended to stringently verify potential modifications by analysis and testing prior to implementation. It is also recommended to try reversible modifications first, so that they can be removed, in case they
show unsatisfactory results.
References
“Ziada, S., Department of Mechanical Engineering, McMaster University Hamilton, Ontario, Canada, Shine, S., Department of Mechanical Engineering, University of Nairobi, Kenya, 1997, ”Strouhal Numbers of Flow-Excited Acoustic Resonance of Closed Side Branches”. Journal of Fluids and Structures, 1999, 127-142. Article No: jfls. 1988-0189.
For more information or discussion, contact us at info@fauske.com . www.fauske.com
#pipe vibration #power plant # plant safety