Adiabatic Calorimetry Testing
Adiabatic calorimetry testing provides data for emergency relief system (ERS) design, safe scale-up of chemical processes, safer process design, and safe transport and storage. Safe design requires knowledge of chemical reaction rates, character and energy release - all of which can be obtained from a low thermal-inertia adiabatic calorimeter such as the VSP2 (Vent Sizing Package 2) or ARSST (Advanced Reactive System Screening Tool). Accelerating Rate Calorimeter (ARC) testing typically has higher thermal inertia and the measured reaction rates are limited and not directly scalable for vent sizing, however the ARC does provide good data for kinetic modeling and thermal stability analysis. A well-equipped process safety lab has all three of these instruments.
The VSP2 and the ARSST measure temperature and pressure under process upset conditions. Adiabatic temperature rise and evolved gas pressure are measured, but of particular importance are the rates of temperature and pressure rise which yield in turn the volumetric rates of vapor and gas generation which must be accommodated by a pressure relief system. (The VSP2 can also be configured to simulate two-phase venting which can occur due to liquid entrainment, and which must be considered when doing vent sizing.) A variety of process upset scenarios can be directly simulated to quantify hazards identified by a PHA or HAZOP study.

Testing Services
VSP2 (Vent Size Package 2) Testing
Best suited for simulating abnormal process "upset" conditions to collect directly scalable data suitable for vent sizing.
Features
The VSP2 is a robust and customizable low thermal inertia calorimeter capable of simulating a variety of unintended process scenarios, including:
- Loss of cooling or agitation
- Accumulation or mischarge of reactants
- Contamination of batch
- Thermally initiated decomposition
Versatile test design makes it easy to study details like resident incubation time and allows for in-situ liquid/gas dosing or sampling
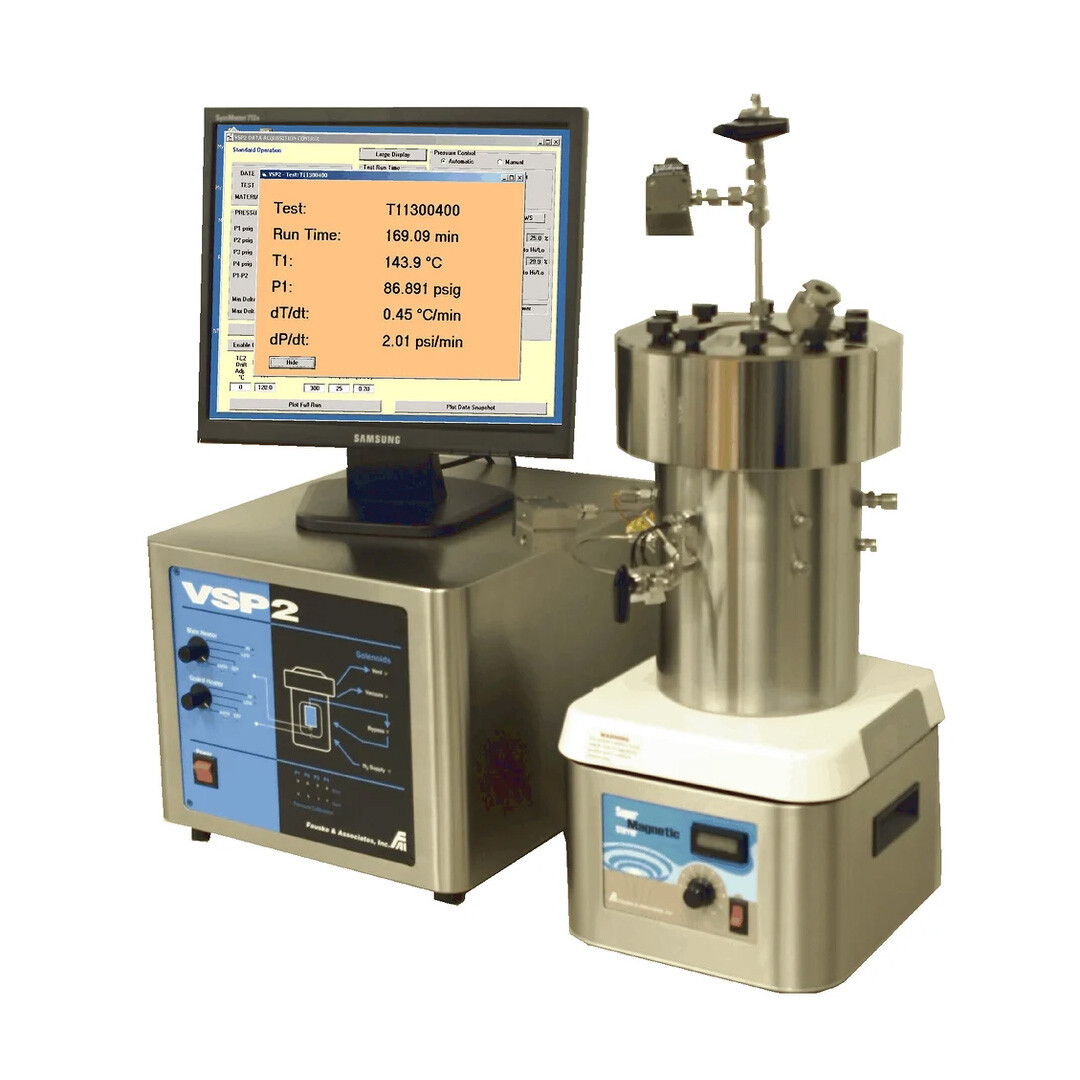
Applications
Use of the VSP2 can help users obtain complete chemical system data:
- Low thermal inertia testing allows data to be directly applied to process scale
- Temperature and pressure rise rates applicable to relief system design are "Based on DIERS two-phase flow technology, recognized by OSHA as an example of “good engineering practice”
- Many testing configurations- Solids, liquids or
two-phase mixtures- Closed or open (vented) tests- Scaled blowdown simulation- Test cells are available in 304 & 316 SS, Hastelloy C, Titanium, and glass-lined - Accurate adiabatic data - Onset temperature- Total adiabatic temperature rise (ΔTad)-
Heat of reaction or mixing- Vapor pressure data - Time-to-maximum -rate (tmr)- Self-accelerating decomposition temperature (SADT) - Relief valve sizing
- Quench tank design
- Effluent handling
- Critical temperature
- Effect of two-phase flow
ARSST (Advanced Reactive System Screening Tool) Testing
Best suited for gas-generating systems, companies with limited sample quantities, and for quickly screening for adverse reactions.
The ARSSTTM enables users to quickly obtain reliable adiabatic data which can be used for a variety of safety applications including characterization of material compatibility, thermal stability and reaction chemistry. Test data includes adiabatic rates of temperature and pressure change which, due to the low thermal inertia, can be directly applied to process scale to determine relief vent sizes, quench tank designs and other relief system design parameters related to process safety management.
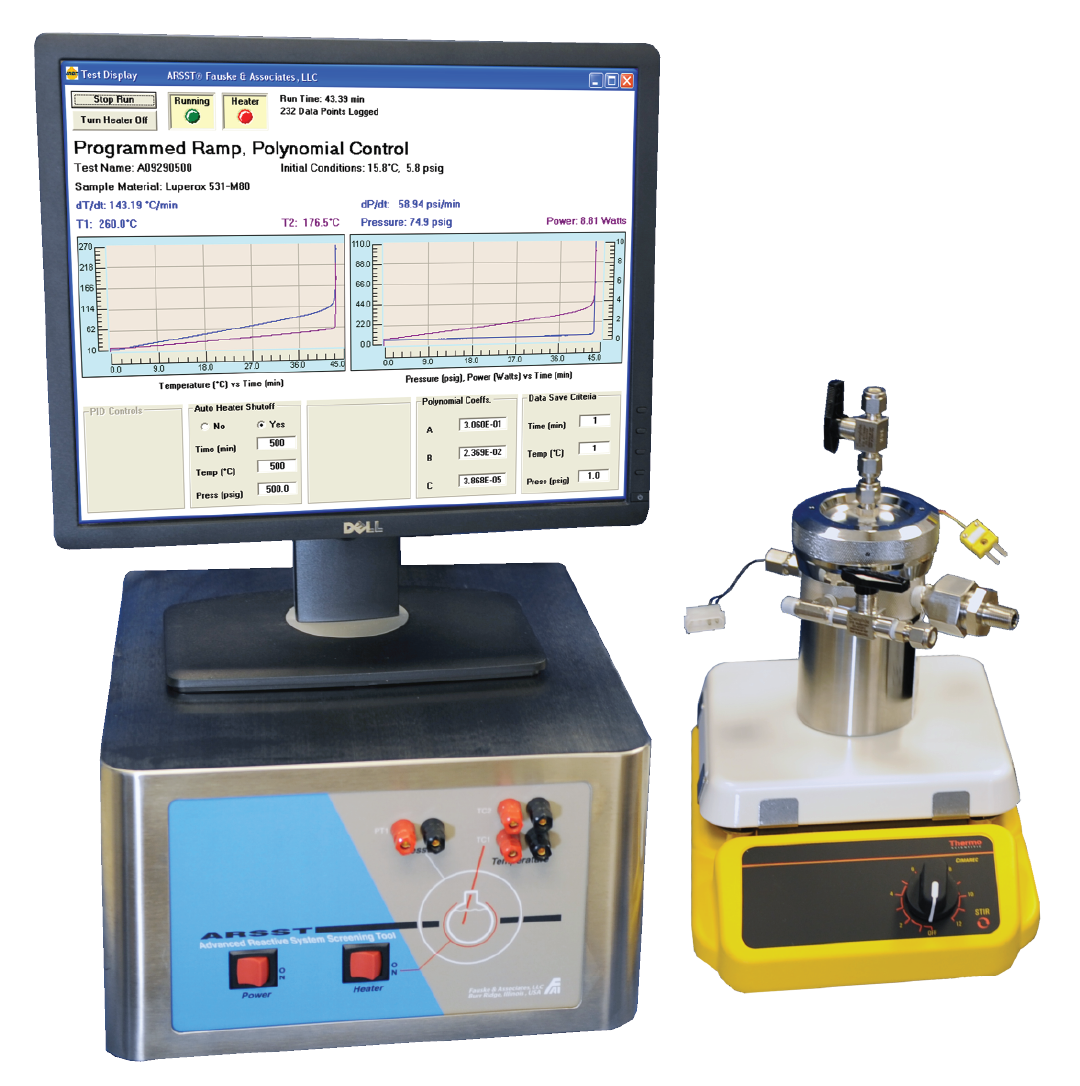
Features
- Small sample size
- Open or closed testing (obtain vapor pressure data from closed cell testing)
- Quickly screen new and existing processes for thermal hazards
- Scanning and isothermal modes
- Reliable results for thermal hazard assessments
- Lightweight glass test cell with good mixing
- Easy setup for fast test turnaround
Applications
- Obtain complete chemical systems data:- Critical temperature- Kinetic parameters
- Estimate process safety parameters including:- Onset temperature- Temperature & pressure rise rates- Adiabatic temperature rise- Heat of reaction and mixing- Tempering temperature- Time to maximum rate (tmr)- Self-accelerating decomposition temperature (SADT)
- Vent sizing
- Emergency relief system design
- Accommodates handling of energetics and pyrotechnics
Accelerating Rate Calorimeter (ARC) Testing
Best suited for identifying potential thermal hazards and early conversion kinetics.
The high thermal inertia adiabatic calorimeter that is used to obtain data regarding the relationships between time, temperature, and pressure for exothermic reactions. The following safety parameters are attained, or can be evaluated, from Accelerating Rate Calorimetery:
- Onset temperature
- Temperature rise rate dT/dt as a function of temperature
- Pressure rise rate dP/dt as a function of temperature
- Adiabatic temperature rise (ATR)
- Heat of reaction
- Adiabatic time to maximum rate (TMR)
- Temperature of no return (TNR)
- Self-accelerating decomposition temperature (SADT)