Nuclear Safety Consulting
Fauske & Associates' Nuclear Services Group is recognized world-wide for comprehensive plant evaluations to help clients enhance the availability and reliability of their operating plants while maintaining regulatory compliance, extending plant life, and reducing operation and maintenance costs in commercial nuclear power plants. We are expert users and developers of the EPRI-owned MAAP computer code (Modular Accident Analysis Program) and offer unique laboratory capabilities in a number of safety related areas.
FAI has a robust quality assurance system to meet stringent requirements required in the Nuclear industry, and have the following certifications:
- ISO 9001
- 10CFR 50 Appendix B
- ISO/IEC 17025
- TickIT
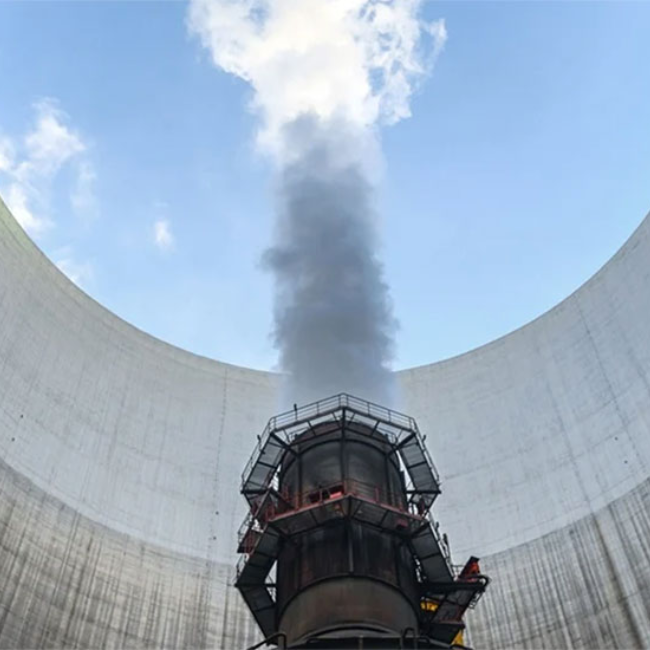
Consulting Experience
Thermal Hydraulic Analysis
Equipment Qualification (EQ) Testing
Probabilistic Risk Assessment (PRA)
Environmental Qualification (EQ)
This is the process of establishing the ability of an equipment to perform its intended function under prescribed operating conditions. This can be established through a combination of tests performed in a laboratory along with calculations.
Commonly performed tests for EQ are:
- Baseline functional test
- Radiation aging
- Post-radiation aging functional test
- Thermal aging
- Post-thermal aging functional test
- Cycle aging
- Post-cycle aging functional test
- Seismic test
- Post-seismic functional test
- High Energy Line Break (HELB) test
- Post-HELB functional test and visual inspection
- Water ingress
Equipment Survivability (ES)
Severe Accident Analysis
Fauske and Associates (FAI) experience in severe accident analysis dates to the original 1980's experiments and computer modeling that led to development of the EPRI-owned MAAP code. FAI was the principal author of the original Severe Accident Management (SAM) Technical Basis Report (TBR) also known as EPRI TR-101869). This report provided the technical bases for development of generic severe accident management guidance (SAMG). In the aftermath of the Fukushima accident, EPRI commissioned an update to the original TBR, and FAI again was a principal author in this update.
Accident Investigation
FAI was founded on expertise in the modeling, evaluation and mitigation of severe (core damage) accidents at commercial nuclear power plants, and has been intimately involved in the international response to the TMI-2, Chernobyl and Fukushima Daiichi accidents.
FAI has over 40 yrs of expertise with the MAAP code (Modular Accident Analysis Program), and other severe accident modeling techniques and tools. We continue to work closely with EPRI and our nuclear utility customers, whether they use MAAP 4, 5, or 6. FAI developed an accident management and training software tool called MARS (Modular Accident Response System) which we have refined into ADEES (Accident Detection and Evaluation System). One of the principal improvements in ADEES is the use of an artificial neural network (ANN) to estimate the state of a severe accident in a pressurized water reactor based on plant signal data.
FAI has collaborated with the nuclear industry in understanding and preparing for severe accidents at power reactors:
- In 1980, FAI contributed to the development of the foundation NSAC-1 report, the first analysis of the TMI-2 accident.
- In 1986, FAI was part of the U.S. mission to Vienna, Austria, where the Soviet Union provided their first technical briefing on the Chernobyl accident to the western European countries.
- In 2011, FAI helped man the “War Room” in Tokyo that was monitoring Fukushima Daiichi (1F) accident progression during the event and considering strategies for accident response and mitigation.
- In 2012, FAI joined the Japanese consortium that was tasked by government agency METI with developing technologies to understand accident progression and the subsequent end-state configuration of Units 1, 2, and 3 at the 1F site. This provided comprehension of key phenomena that are crucial to the fundamental understanding of 1F-specific progression.
Software
We deploy a variety of specialized software such as FATE, RELAP5, MAAP, ADEES, and ANSYS to perform simulations and analyses. Where developing custom software is required, MATLAB, Python, Java, Fortran, and others are used as well.
Decommissioning and Decontamination
Laboratories and Testing Capability
FAI has several fully staffed laboratories with equipment such as a LOCA chamber, a thermal aging autoclave, and a thermal hydraulic loop supporting environmental qualifications, condition assessment, full-scale thermal/hydraulics experiments, and basic physical sciences.