Further Clarification of Non-Equilibrium and Equilibrium Flashing Flows
By Hans K. Fauske, D.Sc., Emeritus President and Regent Advisor, Fauske & Associates, LLC
For chemically reactive systems most emergency releases involve two phase flow. Non-equilibrium conditions are generally required in order to relate the mass flux for flashing flows to local exit conditions. Upstream of the exit region, the flashing process will approach equilibrium conditions if the vent duct is of sufficient length. For flow lengths less than about 100 mm (the non-equilibrium regime) the flashing flow increases strongly with decreasing length, approaching all liquid flow as the length approaches zero (orifice flow).
Non-Equilibrium Flashing Flow
If all liquid exists at stagnation conditions (no vapor), extensive data suggest that a simple length criterion on the order of 100 mm characterizes the residence time (~ 1 ms) requirement for approaching equilibrium flashing flows, which are well described by the Equilibrium Rate Model (ERM) (Fauske, 1985):

where λ is the latent heat of evaporation, vfg is the change in liquid-vapor specific volume, T is the temperature, and C is the liquid specific heat, all evaluated at stagnation conditions. In contrast, the maximum non-equilibrium mass flux as the flow path length approaches zero is given by

where P is the stagnation gauge pressure and ρ is the liquid stagnation density. Considering that

determines the relevant velocity and the length requirement of about 100 mm for all liquid stagnation conditions (near saturated liquid and subcooled liquid).
Equilibrium Flashing Flow
If liquid-vapor (void fraction α > 0.1) exists at stagnation conditions, the length L (mm) required to satisfy a residence time of about 1 ms is given by

and in the case α < 0.1 at stagnation condition, the length increases to L(0.1/α) resulting in length requirements different than 100 mm. In other words the 100 mm length requirement is only relevant to all liquid stagnation conditions.
Length Requirement of 100 mm
It is of interest to note that the simple length criterion of about 100 mm is based on data reflecting a large variation in stagnation pressure from about 2 bara to about 68 bara. Considering Eq. (2) this represents a large variation in the velocity from about 14.6 m s-1 to 134 m s-1. This raises the question, why is there a relatively constant length criterion of about 100 mm, even for high pressure discharge with associated high velocity?
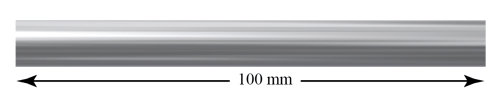
Recalling that in the absence of any vapor at stagnation conditions (xo = 0) the reference to residence time is related to nucleation (the formation of sites where vapor bubbles can grow). This is in contrast to stagnation conditions with vapor (xo > 0) where the residence time relates to vaporization, and where nucleation sites (vapor) already exist.
Note that at 68 bara the superheat relative to atmospheric pressure is 185°C while at 2 bara it is only 20°C, suggesting a ratio of 9.25. It is interesting to observe that this superheat ratio compares closely to the ratio of velocities, 134/14.6 = 9.18.
The relatively constant length criterion of 100 mm is not sensitive to the variation in stagnation pressure (and associated variation in velocity), as a result of the variation in superheat having an equivalent effect on the residence time related to nucleation.
Fauske was named one of the top 10 chemical engineering blogs on the web! Subscribe below and stay up to date on the latest in relief system design, combustible dust, and much more.
Reference
Hans K. Fauske, 1985, "Flashing Flows Or: Some Practical Guidelines for Emergency Releases," Plant/Operations Progress (July, 1985).