Open vs. Closed System Adiabatic Calorimetry: What Are The Differences?
Adiabatic calorimetry is a powerful tool that can be used to support plant safety. A calorimeter is a device that is used to measure the amount of heat associated with chemical or physical processes. An adiabatic calorimeter is designed to ensure that there is no heat transferred between the system and its surroundings. Therefore, an adiabatic calorimeter is designed so that the exothermic heat produced by a reaction directly goes to increasing the temperature of the material. As the temperature increases, the rate of reaction often exponentially increases. On a large plant scale, the available cooling capacity is fixed, so as the rate of reaction exponentially increases, the heat generated from an exothermic reaction can surpass available cooling. This can lead to a runaway reaction. Some common scenarios that may lead to a runaway reaction include fire exposure, loss of cooling, overcharging or a reagent or catalyst, an all-in addition of a reagent, etc. Adiabatic calorimetry can be used to simulate these scenarios to characterize the potential for a runaway reaction and to collect the data necessary for emergency relief system (ERS) design using software such as FERST powered by CHEMCAD. Adiabatic calorimeters measure temperature and pressure increases associated with exothermic reactions, from which the adiabatic rates of temperature and pressure rise are extracted.
Adiabatic Calorimeters
Fauske & Associates utilizes three adiabatic calorimeters: the Accelerating Rate Calorimeter (ARC), The Vent Sizing Package 2 (VSP2), and the Advanced Reactive System Screening Tool (ARSST).
Accelerating Rate Calorimeter (ARC)
The ARC utilizes a 10 ml spherical test cell constructed of stainless steel, Hastelloy C, titanium, or tantalum. Typically ARC testing is conducted in a closed cell mode. Therefore, the pressure generated by a sample must be contained within the test cell. To accomplish this, ARC test cells use heavy walled test cells capable of withstanding pressures up to 3,000 psi or more (and the corresponding high temperatures). As a consequence, the thermal inertia, or phi-factor, of the system is relatively high. The combined mass of the sample and the test cell are kept adiabatic, not just the sample itself. Therefore, a correction to the data must be made prior to applying the data to the large scale. This effectively extrapolates the measured results to higher temperatures beyond the measurable range. While doing this, secondary reactions can be missed. For this reason, care must be taken when applying these data to large scale hazard evaluations. The ARC is typically run in one of two modes of operation, a heat-wait-search mode or an isothermal mode and is typically batch loaded. As in most labs, the ARCs used at FAI have no stirring capabilities and are primarily used for pure component testing. The data collected by the ARC are typically used in ways similar to that collected by thermal stability/screening instruments, and it is not recommended to use ARC data for vent sizing in most cases without detailed understanding of the kinetics, and generally not for gassy/hybrid systems. These limitations to the ARC are the reasons the VSP2 technology was originally developed as the DIERS Bench Scale Apparatus in the 1980’s.
Vent Sizing Package 2 (VSP2)
The VSP2 is a low thermal inertia (i.e. low phi-factor) adiabatic calorimeter capable of simulating abnormal process conditions using either an open or closed cell option. The test cells used are typically 110-120 ml in volume and come in a wide variety of materials of construction and test cell configurations (e.g. baffles for immiscible mixtures, a dip tube for subsurface additions, a closable opening for adding solids prior to performing a closed cell test, etc.). The test cell is thin walled and very lightweight allowing the test to have a low phi-factor. The low phi-factor allows the data to be directly applied to the large scale without making extrapolations, and therefore it is recommended for use in ERS design (i.e., vent sizing). The test cell is fitted with a guard heater (to maintain adiabatic conditions) and an auxiliary heater (for imposing a background heating rate, heat-wait-search, or heating to a target process temperature) and sits in a 3.8-liter containment vessel. For a normal test setup, the reactions can be tracked to above 500°C and nearly 2000 psi (standard rupture disks are set at 1900 psi). A pressure balancing system is used to add or vent nitrogen to/from the containment vessel in order to maintain a minimal pressure difference across the closed test cell wall. This ensures the thin-walled cells do not rupture. Stirring is typically performed using a Super Magnetic Stirrer (capable of stirring up to 10,000 cps) but can also be performed using a mechanical overhead agitator. The VSP2 can be combined with auxiliary equipment, such as an additional containment vessel, cooling coil, syringe pump, or piston to perform a wide variety of tests, and special high-pressure systems are available.
Advanced Reactive System Screen Tool (ARSST)
The ARSST is also a low thermal inertia calorimeter used to obtain critical process upset data. It was developed as a "short cut" alternative the VSP2 testing, sacrificing some capability and versatility for ease of use and a smaller sample size. The ARSST typically utilizes a sample size of 5-10 grams in a lightweight glass test cell with a volume of approximately 10 ml. The test cell is outfitted with a belt heater (used to heat the sample through a preprogrammed thermal scan) and then installed in 350 ml containment vessel. The containment vessel and test cell are easily portable, allowing for the test assembly to be set up in an inert environment (via a glove box) or placed in a freezer prior to testing (for sub-ambient starting temperatures). Tests are normally run using open test cell methodology. In this test configuration, the test cell is open to the containment vessel. Volatilization of the test sample is suppressed by imposing an inert pad gas “backpressure” on the containment vessel (which essentially raises the boiling point beyond the range of the studied reactions). The standard ARSST setup is capable of measuring up to 1,000 psi and the K type thermocouples submerged in the sample can read above 500°C. Table 1 compares and contrasts the three instruments and Table 2 discusses the key advantages and disadvantages of adiabatic calorimetry.
Open vs. Closed System Testing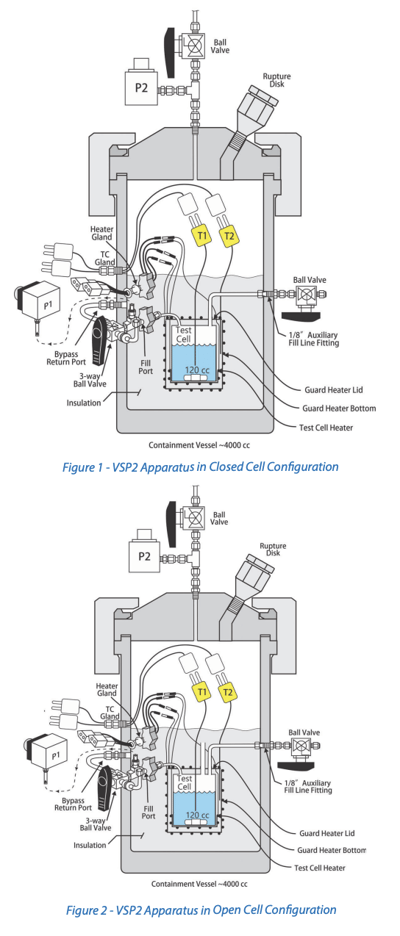
The primary difference between open and closed system testing is the relative headspace volume compared to the sample volume. In open system testing, the test cell is open to a larger closed containment vessel. In these systems, an inert gas backpressure is superimposed on the sample to suppress vaporization of volatiles while allowing noncondensable gas to accumulate safely. Open system testing is ideal for gas generating "gassy" systems (such as decompositions) to ensure there is sufficient volume to accommodate substantial gas accumulation without excessive pressure. In closed system testing, the test cell is isolated from the containment vessel, so the available headspace volume is relatively small and can see very high pressure if a decomposition occurs. Typically, the test cell headspace is evacuated and left under a vacuum. In these cases, the measured test cell pressure represents the vapor pressure of the reacting system. Closed cell tests are ideal for "vapor" dominated systems. Both open and closed system data are valuable and can be used for a variety of purposes. If the goal is vent sizing, oftentimes both open and closed system, or two open-system experiments with different backpressures, are recommended. Figures 1 and 2 illustrate the differences between an open and closed system VSP2 setup.
The key difference in the test results for open and closed system experiments is possibly the peak temperature and pressures measured during the experiment, which can be affected by “tempering” depending on the imposed overpressure in the open test. Tempering in an open test is endothermic due to the latent heat of vaporization and is typically observed as a plateau in in the temperature vs time profile and a corresponding decrease in the temperature rise rate. In a closed system experiment, the measured pressure will follow the vapor-liquid equilibrium of the reacting mixture. The maximum test temperature may be limited if the material has a high vapor pressure. Material will not vaporize and leave the test cell in these experiments. Therefore, tempering of the material will not be observed, and the peak temperatures measured will not be stalled or decreased due to vaporization.
Material will not vaporize and leave the test cell in these experiments. Therefore, tempering of the material will not be observed, and the peak temperatures measured will not be stalled or decreased due to vaporization. However, in closed system experiments, the available void volume is relatively small (and there is uncertainty in the void volume as the density of the material is changing with temperature). This could potentially lead to liquid full conditions at elevated temperatures. If gas generation is occurring, the measured pressure will rapidly increase, potentially rupturing the test cell or prematurely stopping the experiment. In an open system experiment, there is plenty of volume for the gas to equilibrate in, and therefore the measured pressures will be smaller allowing the gas generation to be tracked more completely (and minimizing the possibility of gas forced into solution). This is illustrated by the following equation for converting measured pressure rise rates (P in Pa/s) to gas generation rates (Qg in m3 /s):
Figures 3 and 4 provide a comparison of closed system VSP2 data vs. open system ARSST data with a 300 psig superimposed backpressure. This system was an initiated styrene and methyl methacrylate polymerization. In this case, the temperature rise rates and maximum temperatures are approximately the same indicating tempering did not occur, and we observe the difference in pressure vs. temperature for a closed vs. open system experiment. The closed system experiment starts with a vacuum in the ~30 ml headspace. The open system experiment starts with a 300 psig backpressure in the 350 ml freeboard. The closed system pressure vs. temperature data then follow the vapor pressure of the system. The open system pressure vs. temperature data indicate that significant noncondensable gas was not generated during this experiment.
Further, open system experiments can experience tempering (something very beneficial to our understanding of a runway reaction when sizing an emergency relief system). Material can vaporize and leave the test cell in open system experiments. If there is a volatile component, we would expect to see tempering per the vapor-liquid equilibrium. Therefore, the temperature at which tempering occurs is affected by the initial imposed backpressure. Higher backpressures will suppress vaporization until a higher temperature, allowing the material to react without tempering affecting the temperature rise rates. If the material is nonvolatile (or at least is nonvolatile up to the maximum tested temperature), we would not expect a difference between either the maximum reaction temperatures or the temperature rise rates in open and closed system experiments.
Figure 5 provides an example comparison of data for two open system experiments with different imposed backpressures. The system tested here is a hydrogen peroxide solution decomposition case. We notice that the lower backpressure experiment reaches lower peak temperature rise rates and a lower maximum temperature. This is due to vaporization of the water resulting in tempering of the reaction.
Figure 6 provides an example comparison of data for two open system experiments with different backpressures. The system tested here is a decomposition of 37.5% 3,4,4-trimethyl hexanoyl peroxide in n-dodecane. In this case, we do not observe any differences in the peak temperature rise rates or peak temperatures because there is no vaporization/tempering at these pressures.
Summary
The adiabatic calorimeters mentioned here all are good tools to have in a process safety lab, but it is important to choose the right tool and technique for the task at hand. For example, low phi-factor testing, as in the VSP2 and ARSST, is the generally accepted approach for developing vent sizing data, while ARC data can be useful for studying reaction kinetics. We can observe differences in the maximum temperature, temperature/pressure rise rates, and pressure vs. temperature data for closed vs. open experiments. The reason for these differences (or lack of differences) is driven by the relative void volume and potential vapor pressure of the materials. We can suppress vaporization by applying a pad gas backpressure on the experiment. This in turn allows the experiment to reach higher temperatures before tempering the reaction. If the vapor pressure of a material is very low, or the backpressure is sufficient to suppress vaporization in the temperature range of interest, we do not expect any difference in temperature rise rates or peak temperatures between open and closed cell experiments. We can expect differences in the pressure rise rate and pressure vs. temperature across different sample sizes, containment vessel volumes, and backpressures. Both open and closed system experimental data are useful for vent sizing and extracting other critical safety parameters. It is simply important to review the data with a critical eye and identify potential differences between the experimental setup that could result in differing results. In short, open system experiments are ideal for gas generating materials and closed system experiments are ideal for vapor dominated systems.
Check out these links to learn more:
- Thermal Hazards Evaluation Using the ARSST
- Managing Chemical Reactivity: Minimum Best Practices
- Vent Sizing Applications for Reactive Systems
- Understanding Chemical Safety Instruments: Best Practices