Written by Ashok Dastidar, PhD, Fellow Engineer, VP Dust & Flammability Testing & Consulting, Fauske & Associates LLC
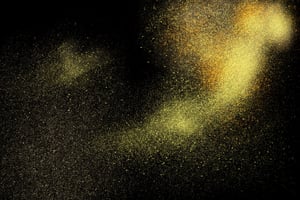
It has been observed that many of the root causes of industrial dust explosions extends back to the awareness of the hazard in the specific process setting. This lack of hazard awareness and inability to identify risks is fundamentally a knowledge-based safety failure. This lack of safety awareness can be easily rectified by a systematic stepwise safety review of the process. This was the logic behind the requirement in NFPA 652 to conduct a Dust Hazards Analysis (DHA) of any process handling combustible dusts so as to identify fire, flashfire and explosion hazards at a facility.
The DHA requirement stems from an earlier recommendation in NFPA 654 to conduct a Process Hazards Analysis (PHA) of powder/dust handling operations. The NFPA felt that the recommendation to conduct a PHA would be confusing to the user of the standard since it may be confused with the requirement to conduct a PHA under the OSHA Process Safety Management (OSHA PSM) program. The intention was not to force companies into a PSM program when such a complex and onerous plan was not warranted. As a result the NFPA, when authoring the new 652 document, changed the term PHA to DHA and made it a requirement; not a recommendation. The requirement in the Standard, which came into effect September 7, 2015, is that every new process has a DHA performed BEFORE it is started up for the first time and existing operations have a DHA completed before September 7, 2018. Additionally, the commodity specific standards; i.e. 654 for general chemicals/plastics, 61 for agricultural dusts, 664 for wood dusts, 484 for metal dusts and 655 for sulfur process, adopted a similar requirement and timeline.
As the 2018 deadline approached it became apparent that many companies, who in good faith, started the DHA process would not be able to meet the timetable and complete the DHAs in time. As a result the NFPA extended the deadline to 2020 to give those companies additional time with the understanding that they would continue to diligently work towards completing the work given the extended time.
Fast-forward to March 2020; many facilities were forced to limit access to their facilities or close down their facilities altogether. With such a global “shutdown” in place, does that mean that the September 2020 extension of the previous deadline will be extended again? No, in recent discussions with several NFPA staff member, their intensions were made clear. The September 2020 extended deadline would not be extended again. This, however, does not mean that Code Enforcers like OSHA, Building and Fire Department inspectors, will be visiting your facility in the autumn. Code Enforcers may choose to issue warnings and not citations or fines until later in the year – however, this is no guarantee and may vary jurisdiction to jurisdiction. As a result, even the current stay-at-home order shutting down facilities it would be a good idea to continue working to meet the September 2020 deadline.
Therefore, given the fact that the facility may be restricted to company personnel only, or may not have current operations actively producing, how can an engineer inspect your facility for compliance to the NFPA standards? The DHA is not only about the site visit but also includes reviews of procedures and equipment design! The DHA team can meet virtually and review documents such as Standard Operating Procedures and practices (housekeeping, hot work, electrical area classification etc.), training records and existing safety audit documents to see if they address combustible dust risks. Getting these documents collected and reviewed will speed up any onsite review that will need to be performed at a later date. One of the many time-sucking pitfalls that can delay a DHA during the on-site visit is the frequent pauses that occur when the audit needs to stop so that relevant or crucial documents or reports can be found and disseminated to the team.
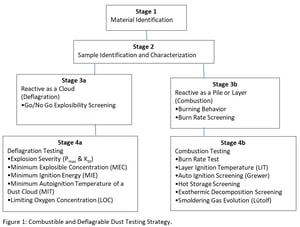
Of these reports that can cause delays, the greatest delay can occur if there is insufficient information available about the combustible nature of the dust(s)/powder(s) the company is processing or generating. The flowchart in Figure 1 is discussed in detail in “Chapter 4 Dust explosions: Test methods” of Methods in Chemical Process Safety vol. 3 Dust Explosions. It is also discussed in a presentation titled “Introduction To Combustible Dust Test Methods” at the Digital Dust Safety Conference February 24-27, 2020 and addressed in the webinar “Schema for Combustible Dust Testing to Provide Data for a Dust Hazards Analysis (DHA)” presented on March 31, 2020. The flowchart discusses the types of tests that can be used to characterize a potentially hazardous dust for explosibility and combustibility. Each of the tests described in the chart has merit for establishing dust safety hazards by establishing explosion/combustion violence and the ease at which the dust will undergo this hazardous reaction. The information may be necessary for all the dusts/powders handled at the plant and all the data from the various tests may be required. The process of collecting the sample, contracting the tests and obtaining the data will take several weeks thus delaying the delivery of the final DHA report. However, the DHA on-site team can review the process flow and estimate the number of samples that need to be tested and what subset of the tests identified in Figure 1 need to be conducted before the field visit and which ones can be deferred to a later time.
Ultimately, it is important to start the DHA process now, even though the actual field visit will need to be conducted later, the documentation can be reviewed and the test data obtained (with time to fill gaps in either).
For further information, or if you would like assistance with your DHA and Combustible Dust Hazards Training Program, please email DHA@fauske.com or contact us below: