Nuclear Capabilities - Fauske & Associates
Cable Health and Aging Management Cable Testing Chemical and Radioactive Waste Safety Commercial Grade Dedication / Reverse Engineering and Obsolescence Custom Engineering & Testing Debris Intrusion Electromagnetic Radiation (EMC) Equipment Qualification (EQ) Testing Fire Modeling & Cable Selection/ Circuit Analysis Post-Fukushima Engineering and Activities Gas / Air Intrusion Accumulation MAAP - Modular Accident Analysis Program Plant Analysis Probabalistic Risk Assessment (PRA) RELAP Transient Analysis Reactor Auxiliary Building Analysis Seismic Walkdowns Severe Accident Management Spent Fuel Processing Engineering Structural Engineering Thermal Hydraulics Verification and Validation (V&V) Waste Management, Decontamination & Decommissioning (D&D) Process Engineering Water Hammer Solutions and Testing
Table of Contents
FAI software - nuclear plant safety solutions

Modular Accident Analysis Program (MAAP)
Since the events at Fukushima, there has been increased interest to expand current simulator capability to address severe accidents. The Modular Accident Analysis Program (MAAP), an Electric Power Research Institute (EPRI) owned and licensed computer software, was developed to simulate and study severe accidents. MAAP is an integral code simulating both containment and primary system during severe accidents. Fauske & Associates (FAI) has been under contract to improve MAAP models related to BWR primary system, lower plenum, instrument tubes, molten core concrete interaction and others in order to better follow the severe accident at Fukushima.
Simulators can be expanded to cover severe accidents by implementing the MAAP code into the existing simulator. This implementation using MAAP4 was done for Krsko in Slovenia and Ulchin in Korea. MAAP5 was implemented for Daya Bay in China and Kori in Korea.
MAAP5 PWR code can be a good thermal hydraulic engine for PC based simulator for severe accident training.
According to Chan Young Paik, PhD, Vice President of Methods Development for FAI : "The MAAP5 PWR code is the latest generation of MAAP implementing new models to calculate forced and natural circulation inside a reactor coolant system (RCS) with more detailed nodalization, point kinetic and 1-D neutronics models, features to address details of new advanced reactor designs such as AP1000 and EPR, and improved containment models." "Improvements were also made to include a steam header model with detailed steam dump logic so that the code can calculate initial RCS and steam generator responses after a reactor scram," continues Dr. Paik. "In addition, MAAP5 has improved models for shutdown states such as modeling nozzle dams in the RCS loops, mid-loop operation, and reactor head open with the vessel submerged under the refueling water pool."
MAAP5 code can also calculate the ANS-3-5 transients required for simulators. These transients include a manual reactor trip, simultaneous trips of feed water pumps, simultaneous closure of all MSIVs, trip of any single reactor coolant pump (RCP), loss of coolant accidents, main steam line break, maximum power ramp, and maximum design load rejection.
FATE™
Using FAI developed FATE™ software, we can calculate temperatures, pressures, flow rates and compositions for fluids, gases and structures associated with waste management process D&D. It is uniquely suited to nuclear facility operations because it combines models for fluid flow and heat transfer with models for aerosol transport and deposition, explosions and fire. FATE™ has been applied to dozens of United States Department of Energy (DOE) and commercial nuclear applications and its predecessor code was awarded a DOE Silver Award for Technology Innovation at Hanford.

Modular Accident Response System (MARS™)
The Modular Accident Response System (MARS™) is a software suite that monitors and predicts potential future states of a nuclear power plant under abnormal and accident conditions. MARS™ is used to:
- Demonstrate the effectiveness of procedures
- Support accident management
- Train on reactor response to accident conditions
- Generate emergency planning scenarios
- Predict the potential time of core damage during an accident
MARS™ software was created by Fauske & Associates (FAI), a Westinghouse affiliated company, under the Westinghouse/FAI Quality Assurance (QA) program, and has been in use by customers for nearly 20 years. Description.
The MARS™ software suite uses engineering software to predict future plant conditions much faster than in real time, predicting many hours ahead in just a few minutes. MARS™ can operate either online or offline. In the online mode of operation, the system gathers information from the plant process computer (or related system) to obtain a snapshot of the plant conditions. This snapshot includes information such as temperatures, pressures and water levels throughout the primary, secondary (for pressurized water reactors) and containment systems.
The MARS™ suite includes:
- A solid engineering simulation of the nuclear power plant
- The ability to use “live” online plant data for engineering simulations and/or offline data
- Software simulation models to represent operator actions following their procedures
- A user-friendly graphical user interface representing the nuclear power plant
- Engineering models for emergency response activities (for example, off-site radiation dose assessment)
FAI’s Nuclear Waste Technology D & D Includes:
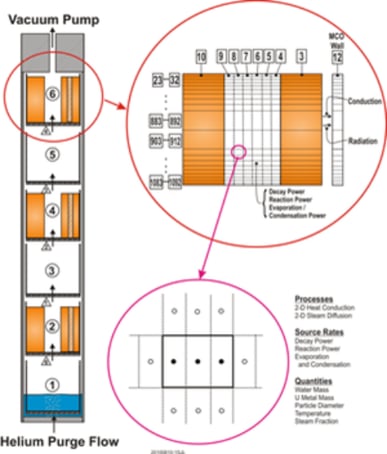
Metallic spent nuclear fuel vacuum drying model
- FATE™ software for process and facility design and safety calculations
- Facility flow, heat transfer and toxic/radiological materials transport
- Predict thermal stability during waste processing, shipping and storage
- Manage flammable and explosive hazards
- Facility fire analysis including toxic/radiological effects
- Chemical reaction propagation limits, including pyrophoricity
- Flammable gas generation by chemical reactions and radiolysis
- Aerosol generation, transport, deposition and removal
- Facility emissions and source terms for processes, accidents and D & D
- Emergency preparedness
Experimental Facilities for Hazard Quantification
• Lab-scale equipment for measuring chemical reaction, heat-up and pressurization rates
• Fluid systems testing, including waterhammer and flow regime
• Chemical and thermal behavior during waste processing, shipping and storage
• Gas and vapor flammability limits
• Vent design validation for managing flammable gas (H2)
• Dust explosion and hybrid dust/gas systems
• Kinetics of decomposition and chemical reactions
- Provides a consistent framework for modeling a wide dynamic range of common Department of Energy (DOE) and commercial fuel and waste applications including:
- Treatment, and storage of defense waste, including metal
- Drying of commercial oxide fuel
- Reactor building fire modeling or fire PRA
- Hydrogen release, transport and flammability for post-Fukushima
- FATE software predecessor code HANSF won a DOE innovation award (FY2000)
- FATE is developed and maintained under a NQA-1 Quality Assurance Program
(double bore-hole arrangement with single filter)
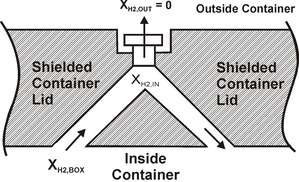
An Interview with Fauske & Associates
Nuclear Services Manager Jacky Shoulders
Fauske & Associates is important in the nuclear industry starting with the history and background of FAI in the nuclear industry and why that is significant is because it goes back to 1980 with our current emeritus president Hans K. Fauske starting FAI.
We focused in two different areas - testing and nuclear. We started out with a very good understanding, with Dr. Bob Henry of the needs of the nuclear industry such as waterhammer, air intrusion and into piping systems. It has evolved over the years to include many different software. We have a severe accident analysis code called MAAP that we developed and EPRI owns.
We use it worldwide to do a severe accident analysis that feeds into severe accident management guidelines for nuclear power plants all over the world. We also utilize the RELAP code here and have done testing to back these items up and the conclusions that we come to and that waterhammer testing has allowed us to run these codes with confidence and provide these two different utilities mainly in the United States but there are a few all over the world.
When waterhammers are detected we can test and we can run these simulations and provide solutions for our customers for following up with that on the back end of the lifecycle for nuclear you have the waste technology group that performs hydrogen deflagration, calculations to determine you know make sure that the waste is sitting safely and can be transported safely and also we use the FATE code there to determine accident analyses from a hydrogen production perspective which is done during a severe accident in a nuclear power plant. So, the experiences widespread back, like I said, to the early 80s and we still hold a lot of that expertise today.
We also have our chemical side of the business - in chemical processing and chemical safety, how do you see the nuclear side of it complementing those things?We definitely work with our chemical brothers on the other side of the house we are we are all one Fauske so nuclear- chemical we're all one company serving the greater good of the company so we've interacted a lot with the flammability group, the thermal hazards groups for relief sizing, we've done non detonation calculations to determine pressure waves against fire doors, etc, things of that nature. With our expertise over here with traveling waves - acoustical waves that has melded very well with our relief sizing and detonation testing.
When you think about all the way back to Chernobyl and to Fukushima and then some, we've been involved in so many different aspects of nuclear and chemical safety, how do you feel we complement the larger Westinghouse Corporation and do we work in tandem with them quite a bit?Absolutely. We have our Probabilistic Risk Assessment brothers up at Westinghouse that we put inputs to from our MAAP codes. We work very well with that group. We've also got the RELAP people in Westinghouse that help us do reviews or author some of the calculations and we'll do the reviews so we are a kind of third-party reviewer for some Westinghouse efforts and we also work hand-in-hand with them with their PRA groups. We can also pull from the Greater Westinghouse resources and complete a project for a customer as a turnkey project. It is cradle to grave, all-encompassing project for the customer so they don't have to go to different vendors. They can come to Westinghouse and Fauske and complete this project.
It’s nice to have a one-stop shop for an extreme level of expertise in a variety of areas…Yes, it helps our customers. That way, on the administrative side they only put one contract out, they get one offer, they only get one set of the project management support and things like that and then that gets it taken care of – a one-stop shop.
What about innovations? Is there anything that we're working on currently that comes to mind?Absolutely, a lot of our innovations, for example, we're not a software development company per se but we do a lot of software development. We’re developing modifications for the FATE code that we're getting quality assured so we can use it in nuclear safety applications for the MAAP group as we continue to do development and modules there at EPRI’s direction. So, our innovation here is just improving on what we currently have. We also have the SSTDR - it's a Spread Spectrum Time-Domain Reflectometry analysis, so basically in our electrical field we are partnered with EPRI to do some testing and analysis for the SSTDR and that is going to be a new online monitoring system for cables and electrical systems. So, we're helping EPRI with their innovation efforts there, in that.
If you had to give the elevator speech of Fauske & Associates, particularly in the nuclear side, what would you say? How would you describe us in a nutshell, if possible?In a nutshell, our expertise is broad. We are expert in severe accident analysis, we're water hammer and testing experts for many different areas. We can be a one-stop shop if so desired to bring in our Westinghouse resources and provide the best quality deliverable for our customers to meet their needs in this ever-changing world.
FAI Chernobyl History
Robert E. Henry, PhD, Emeritus Senior Vice President and Regent Consultant at Fauske & Associates was one of the U.S. Delegates selected to attend the international meeting at the International Atomic Energy Agency (IAEA) headquarters in Vienna, Austria. Since the IAEA is part of the United Nations (UN), this was the location selected for the USSR experts to explain what caused the accident, as well as what actions were taken during the aftermath. This three day presentation was entitled “Accident at The Chernobyl Nuclear Power Plant and Its Consequences” and the briefing revealed the design and operational flaws responsible for the accident. As with all accidents, it is essential to learn from the accident conditions and the long term stabilization of the core material even when the designs are greatly different from those in the U.S.
“The design for the RBMK (reaktor bolshoy moshchnosty kanalny, high-power channel reactor) nuclear power plants that were built in the Soviet Union differed considerably from the commercial nuclear power plants built in the rest of the world,” states Dr. Henry. “Because of the Cold War, we had only a sketchy idea of the RBMK designs and how they were operated prior to the event. In those days, if we traveled abroad, we were always asked if you had contact with anyone from the Iron Curtain countries.
To illustrate the substantial differences in the designs, for the light water reactors that are built, licensed and operated in the U.S. and elsewhere, water cools the reactor core and also moderates the nuclear reaction. Hence, the water is an essential component of the nuclear reaction and if water were to be removed from the core as the result of an accident condition, the nuclear reaction will be inherently shutdown. Conversely, for the RBMK design, water is used to cool the reactor core inside of almost 1700 pressure tubes, but the nuclear reaction is moderated by graphite blocks which surround the pressure tubes. Therefore, water is a poison to the nuclear reaction for this design and, if water is removed from the core by an accident condition, the nuclear reaction intensifies and the power generated in the core increases rapidly. An increase in the core power acts to reduce the water inventory in the core at a faster rate resulting in further increases in core power. This characteristic is known as a positive void coefficient for the nuclear fission reaction. As a consequence of this core design characteristic, the accident that occurred in Chernobyl Unit 4 reactor was the first ever runaway nuclear reaction in a power plant, with the core power increasing exponentially to about 500 times the maximum design value over an interval of approximately 20 seconds."
This accident resulted from a desire to use the energy of a coasting-down turbine to power water injection into the reactor core if an accident condition were to result in a loss of electrical power to the plant. To investigate the real plant response, USSR scientists and engineers decided to test this concept on one of their plants. The intent was to initiate a loss of power transient for a reactor that was about to be shut down for refueling. As the reactor was in the process of being shut down and prepared for the test, the Kiev power dispatcher requested more power from the site and the reactor power had to be increased for a period of time." Continues Dr. Henry, "A return to power from the plant state was complicated and the manner in which it was accomplished led to the violation of procedures that were in-place for safe operation of the plant. Another complicating feature leading up to the accident was that the test to be conducted was on the plant electrical equipment, so an electrical engineer was in charge, in the control room, for the test to be conducted that night. He had no understanding of the reactor core configuration caused by the return to power, the influence of a 'positive void coefficient', etc.
Another difference between the RBMK design and those used in the United States and elsewhere is the protection of a high pressure leak-tight containment building that surrounds the nuclear core and the reactor cooling system. A high pressure leak-tight containment is an important aspect of the plant design and licensing evaluations in the western world, but this was not part of the design for the Chernobyl plants. Therefore, the runaway power escalation rapidly over-pressurized the reactor coolant system such that it burst open, discharging the nuclear fuel and radioactive fission products into the surrounding environment. The gaseous and aerosolized fission products were ejected high into the air above the plant and these circulated to the north over the next two and a half days until an engineer walked in from the parking lot and into the Forsmark plant on a rainy Monday morning in Sweden. On entering the plant, he set off the plant radiation alarms because his shoes picked up radioactive iodine and cesium fission products that had been captured by the rain as they passed overhead. This was the first that the western world knew of the nuclear accident in the USSR and at the Chernobyl site specifically. When the satellite cameras were reviewed early on Saturday morning of April 26th, 1986, the flash from the bursting of the reactor coolant system and the discharged of fuel bundles out of the plant building could be seen from space.
Radioactive fission products from the Chernobyl were detected in the air in the Iron Curtain countries and Italy, France, Germany, Sweden and others. In fact, the radiation level in Harrisburg, Pennsylvania due to the Chernobyl accident was three times higher than peak observed from the TMI-2 accident in 1979. Fear of the unknown is a powerful emotion and it caused milk and food to be confiscated in some counties and also resulted in the shutdown of the one nuclear plant that was operating in Italy at the time as well as the stoppage of construction of one that was being built."
Following the TMI-2 and Chernobyl accidents, Fauske and Associates assisted a number of U.S. utilities, including Commonwealth Edison in the evaluations of individual commercial nuclear plants with respect to their defensive-in-depth capabilities for a large range of accident scenarios. The results of these studies were entitled Individual Plant Examinations (IPEs) and they were submitted to the Nuclear Regulatory Commission (NRC) for their review. Most of these were eventually expanded into full Probabilistic Safety Assessments (PSAs). In addition, in the early 90’s, FAI was selected by Electric Power Research Institute (EPRI) to formulate the Technical Basis Report that characterized the status of the important phenomena that could occur during a core damage event in a sufficient manner to formulate Severe Accident Management Guidelines (SAMGs) for both Boiling Water Reactor (BWR) and Pressurized Water Reactor (PWR) designs and all types of high pressure leak-tight containments. As part of this, a new version of the Modular Accident Analysis Program (MAAP) code (MAAP4 and later, MAAP5) was chartered to support the evaluations of SAMGs for different designs for a large spectrum of accident conditions. All of these have added to increase the defense-in-depth for protection against accident conditions that could result in overheating of reactor cores.